Preparation method of sodium sulfide
A technology of sodium sulfide and raw coal, applied in alkali metal sulfide/polysulfide, chemical industry, sustainable manufacturing/processing, etc., can solve the problem of incomplete reaction of mirabilite, pulverized coal, incomplete calcination of pulverized coal, and output of sodium sulfide Low and other problems, to achieve the effect of improving the conversion rate of raw materials, reducing the content of SO2, and reducing the content of SO2
- Summary
- Abstract
- Description
- Claims
- Application Information
AI Technical Summary
Problems solved by technology
Method used
Examples
Embodiment 1
[0015] A method for preparing sodium sulfide, comprising the steps of:
[0016] a. Put the raw coal into the ball mill and grind it into powder, then add the raw coal powder and sodium sulfate into the mixer, mix and stir evenly, and get the mixture for later use, wherein the raw coal powder and sodium sulfate are added in a ratio of 1:2 ;
[0017] b. Spray the mixed material that has been stirred into the calciner, maintain the slight negative pressure atmosphere in the calciner, so that the calcining temperature is maintained at 1000 ° C, and the calcining time is 30 minutes to obtain a sodium sulfide alkali billet for use;
[0018] c. The sodium sulfide alkali billet is melted into a liquid by heat, and the alkali billet is washed with water into a solution with a sodium sulfide content greater than 300g / L, and left to stand for purification and clarification for 20 hours to obtain a reduction leaching solution;
[0019] d. Evaporate the leaching solution to about 250g / L t...
Embodiment 2
[0023] A method for preparing sodium sulfide, comprising the steps of:
[0024] a. Put the raw coal into the ball mill and grind it into a powder, then add the raw coal powder and sodium bicarbonate into the mixer, mix and stir evenly, and get the mixture for later use, wherein the raw coal powder and sodium bicarbonate are added in a ratio of 1:2.5 ;
[0025] b. Spray the mixed material that has been stirred into the calciner, maintain the slight negative pressure atmosphere in the calciner, so that the calcining temperature is maintained at 1020°C, and the calcining time is 35min, so as to obtain a sodium sulfide alkali billet for use;
[0026] c. The sodium sulfide alkali billet is melted into a liquid by heat, and the alkali billet is washed with water into a solution with a sodium sulfide content greater than 300g / L, and left to stand for purification and clarification for 25 hours to obtain a reduction leaching solution;
[0027] d. Evaporate the leaching solution to ab...
Embodiment 3
[0031] A method for preparing sodium sulfide, comprising the steps of:
[0032] a. Put the raw coal into the ball mill and grind it into a powder, then add the raw coal powder and sodium bicarbonate powder into the mixer, mix and stir evenly, and get the mixture for later use, wherein the raw coal powder and sodium bicarbonate powder are added in a ratio of 1:3 ;
[0033] b. Spray the mixed material that has been stirred into the calciner, maintain the slight negative pressure atmosphere in the calciner, so that the calcining temperature is maintained at 1050° C., and the calcining time is 40 minutes to obtain a sodium sulfide alkali billet for use;
[0034] c. The sodium sulfide alkali billet is melted into a liquid by heat, and the alkali billet is washed with water into a solution with a sodium sulfide content greater than 300g / L, and left to stand for purification and clarification for 30 hours to obtain a reduction leaching solution;
[0035] d. Evaporate the leaching so...
PUM
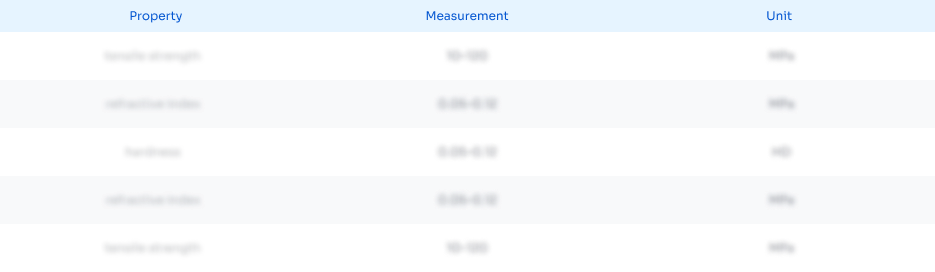
Abstract
Description
Claims
Application Information

- R&D Engineer
- R&D Manager
- IP Professional
- Industry Leading Data Capabilities
- Powerful AI technology
- Patent DNA Extraction
Browse by: Latest US Patents, China's latest patents, Technical Efficacy Thesaurus, Application Domain, Technology Topic, Popular Technical Reports.
© 2024 PatSnap. All rights reserved.Legal|Privacy policy|Modern Slavery Act Transparency Statement|Sitemap|About US| Contact US: help@patsnap.com