Quenching-tempering heat treatment method for large-scale module die steel
A heat treatment method and mold technology, which are applied in the field of water quenching and air quenching and tempering heat treatment technology, can solve the problems of high cooling strength and easy cracking in water quenching, impermeability in oil quenching, and easy cracking in water quenching, so as to eliminate the stress of surface structure transformation. , to avoid cracking, the effect of slowing down the cooling rate
- Summary
- Abstract
- Description
- Claims
- Application Information
AI Technical Summary
Problems solved by technology
Method used
Image
Examples
Embodiment Construction
[0023] pass below Figure 1 ~ Figure 2 As well as listing some optional embodiments of the present invention, the technical solutions (including preferred technical solutions) of the present invention are further described in detail. Apparently, the described embodiments are only some of the embodiments of the present invention, not all of them. Based on the embodiments of the present invention, all other embodiments obtained by persons of ordinary skill in the art without creative efforts fall within the protection scope of the present invention.
[0024] The quenching and tempering heat treatment method of large modular mold steel designed by the present invention comprises the following steps:
[0025] S1, warming up, as figure 1 Shown: Use steps to raise the temperature to 870°C±10°C, first raise the temperature to 650°C at a heating rate of ≤80°C / h, then hold for 3 hours, and then raise the temperature to 870°C±10°C at a heating rate of ≤100°C / h.
[0026] S2, heat pres...
PUM
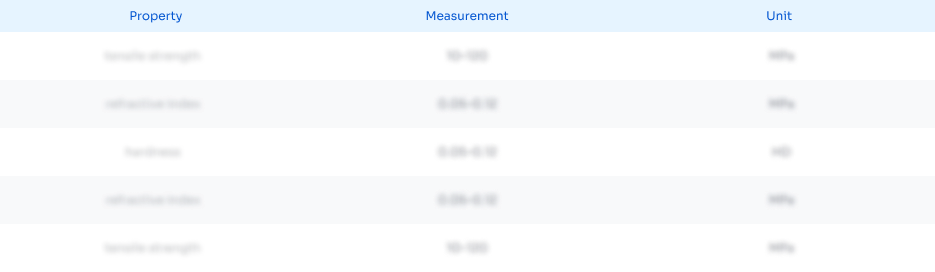
Abstract
Description
Claims
Application Information

- R&D Engineer
- R&D Manager
- IP Professional
- Industry Leading Data Capabilities
- Powerful AI technology
- Patent DNA Extraction
Browse by: Latest US Patents, China's latest patents, Technical Efficacy Thesaurus, Application Domain, Technology Topic, Popular Technical Reports.
© 2024 PatSnap. All rights reserved.Legal|Privacy policy|Modern Slavery Act Transparency Statement|Sitemap|About US| Contact US: help@patsnap.com