High polymer material continuous treatment method and device
A technology for polymer materials and processing equipment, which is applied in the field of continuous processing of polymer materials, and can solve problems such as equipment structure limitations and inability to meet market demands.
- Summary
- Abstract
- Description
- Claims
- Application Information
AI Technical Summary
Problems solved by technology
Method used
Image
Examples
Embodiment 1
[0034] Such as figure 1 As shown, the polymer material continuous processing equipment of the present invention includes a processing furnace 1, a steam generator 2, a transmission mechanism 3, an exhaust system 4, a cooling device 5, an oil-water separator 6, an air storage tank 7, and a temperature control system 8 And the steam heating pipeline 9, the saturated steam output end of the steam generator 2 is connected with the treatment furnace 1, the cracked carbide output end of the transmission mechanism 3 is connected with the treatment furnace 1, and the pyrolysis combustible gas water vapor output end of the transmission mechanism 3 passes through The exhaust system 4 is connected to the cooling device 5, the output of the cooling device 5 outputs combustible gas and is connected to the input of the gas storage tank 7, the output of the gas storage tank 7 is connected to the processing furnace 1, and the superheated steam output of the processing furnace 1 The input end ...
Embodiment 2
[0038] The present invention uses superheated steam as a heating heat source and an oxygen-insulating medium, and controls the temperature in the transmission mechanism 3 and the treatment furnace 1 so that the high-temperature superheated steam is used for oxygen-free thermal decomposition of the polymer material during the transmission process, and the polymer material is in the absence of oxygen. Oxygen high-temperature superheated steam does not burn, oxidize, and produce harmful gases such as dioxin and carbon dioxide, and effectively decomposes polymer components such as resins, curing agents, and adhesives in polymer composite materials, and some materials that cannot be cracked can be damaged. Recycle. Specifically, anaerobic or micro-oxygen (oxygen content≤0.3%) superheated steam at a temperature of 450-600°C is introduced into the conveying mechanism 3, and the conveying mechanism 3 and the processing furnace 1 are kept in a slight negative pressure state by using the...
PUM
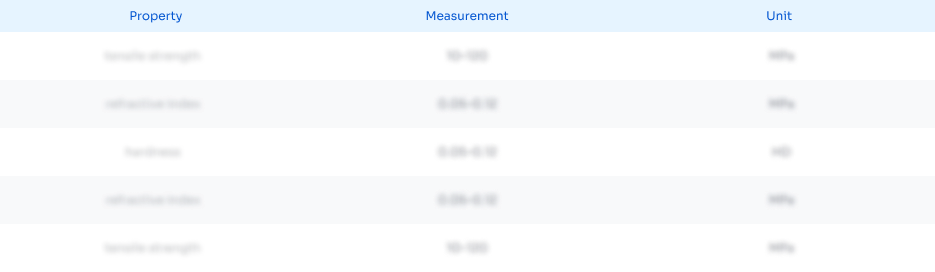
Abstract
Description
Claims
Application Information

- R&D
- Intellectual Property
- Life Sciences
- Materials
- Tech Scout
- Unparalleled Data Quality
- Higher Quality Content
- 60% Fewer Hallucinations
Browse by: Latest US Patents, China's latest patents, Technical Efficacy Thesaurus, Application Domain, Technology Topic, Popular Technical Reports.
© 2025 PatSnap. All rights reserved.Legal|Privacy policy|Modern Slavery Act Transparency Statement|Sitemap|About US| Contact US: help@patsnap.com