Concrete mortar
A concrete mortar and mixing technology, applied in the field of mortar, can solve the problems of poor toughness and mechanical properties, easy hollowing and cracking of mortar, etc., achieve the effect of improving toughness and mechanical properties, solving easy cracking, and improving adsorption performance
- Summary
- Abstract
- Description
- Claims
- Application Information
AI Technical Summary
Problems solved by technology
Method used
Examples
preparation example Construction
[0029] Preparation of lignite treatment: Take lignite and pulverize it in a pulverizer, pass through a 100-mesh sieve, take the sieved particles and move them into the muffle furnace, pass nitrogen protection into the furnace at a rate of 60-80mL / min, and pass through the furnace at a rate of 6-10°C / min Program temperature rise to 550~650°C, heat preservation for 2~4 hours, heat up to 800~900°C, heat preservation for 3~5 hours, then cool down to room temperature with the furnace, discharge the material, and obtain the pyrolysis material, calculated in parts by mass, Take 30~50 parts of pyrolysis material, 8~10 parts of petroleum resin, 4~6 parts of β-terpene resin, 0.8~1.2 parts of nano-iron powder in the container and mix them in a container, and pass nitrogen protection at a rate of 10~20mL / min. 180~220°C, heating and stirring for 45~60 minutes, then naturally cooling to room temperature to obtain the processed lignite.
[0030] The preparation method of composite modified p...
PUM
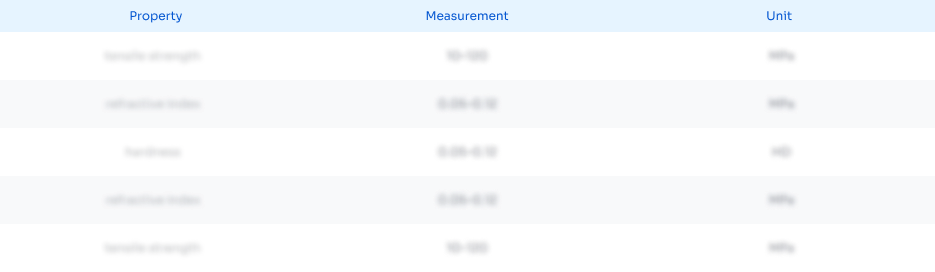
Abstract
Description
Claims
Application Information

- R&D
- Intellectual Property
- Life Sciences
- Materials
- Tech Scout
- Unparalleled Data Quality
- Higher Quality Content
- 60% Fewer Hallucinations
Browse by: Latest US Patents, China's latest patents, Technical Efficacy Thesaurus, Application Domain, Technology Topic, Popular Technical Reports.
© 2025 PatSnap. All rights reserved.Legal|Privacy policy|Modern Slavery Act Transparency Statement|Sitemap|About US| Contact US: help@patsnap.com