SEBS (Styrene-Ethylene-Butylene-Styrene) composite material for slippers as well as preparation method and application thereof
A technology of composite materials and slippers, applied in applications, footwear, clothing, etc., to achieve the effects of improving comfort, broad market prospects, and improving poor elasticity
- Summary
- Abstract
- Description
- Claims
- Application Information
AI Technical Summary
Problems solved by technology
Method used
Image
Examples
preparation example Construction
[0041] The preparation method of the above-mentioned SEBS composite material for slippers of one embodiment, comprises the following steps:
[0042] S10: Mix SEBS, white oil, lubricant, antioxidant and ultraviolet absorber in proportion to obtain a mixture.
[0043] S20: Add the mixture into the internal mixer for the first internal mixing, and then add the foaming agent for the second internal mixing.
[0044] Specifically, the mixture in step S110 is added to the internal mixer at 110°C-120°C for the first time, and after 5-10 minutes, when the temperature rises to 130°C-160°C, a foaming agent is added for the second time. For the second banburying, the time for the second banburying is 1-8 minutes.
[0045] S30: extrude the mixed material after banburying in a single-screw extruder.
[0046] The mixed material after banburying in step S20 is extruded in a single-screw extruder, wherein,
[0047] It should be noted that step S10 and step S20 may also be performed simultan...
Embodiment 1
[0052] (1) 40 parts of SEBS with a weight-average molecular weight of 90,000, 20 parts of white oil, 5 parts of zinc stearate, 5 parts of stearic acid, 5 parts of oleic acid amide, 1 part of antioxidant 1010, and 1 part of ultraviolet absorber were prepared. Mixed to obtain a mixture, and the mixture was added to an internal mixer at 110 ° C for the first internal mixing. After 5 minutes, 3 parts of azodicarbonamide were added, and the second internal mixing was carried out at 140 ° C. The time is 5 minutes.
[0053] (2) The mixed material after banburying is extruded through a single-screw extruder at 210°C, and the average particle size of the pellets obtained by extrusion is about 25 mm.
[0054] (3) Putting the extruded pellets into an injection molding machine for one-time molding to obtain slippers, wherein the injection molding temperature is 220°C.
[0055] Wherein, the preparation method of SEBS is:
[0056] (1) Under the protection of high-purity nitrogen, 500g of cy...
Embodiment 2
[0061] (1) 40 parts of SEBS with a weight-average molecular weight of 200,000, 20 parts of white oil, 5 parts of zinc stearate, 5 parts of stearic acid, 5 parts of oleic acid amide, 1 part of antioxidant 1010, and 1 part of ultraviolet absorber were prepared. Mixed to obtain a mixture, and the mixture was added to an internal mixer at 110 ° C for the first internal mixing. After 5 minutes, 3 parts of azodicarbonamide were added, and the second internal mixing was carried out at 140 ° C. The time is 5 minutes.
[0062] (2) The mixed material after banburying is extruded through a single-screw extruder at 210°C, and the average particle size of the pellets obtained by extrusion is about 25 mm.
[0063] (3) Putting the extruded pellets into an injection molding machine for one-time molding to obtain slippers, wherein the injection molding temperature is 220°C.
[0064] Wherein, the preparation method of SEBS is:
[0065] (1) Under the protection of high-purity nitrogen, 500g of...
PUM
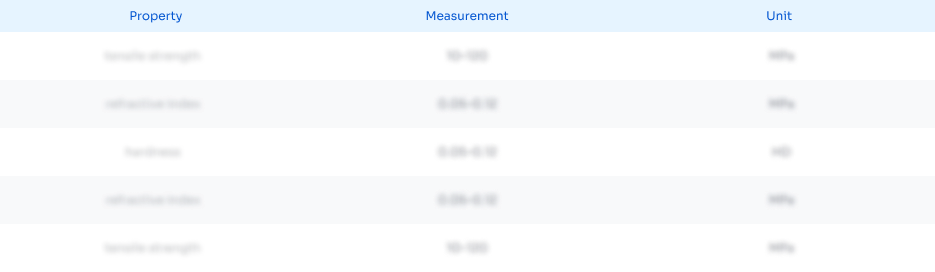
Abstract
Description
Claims
Application Information

- Generate Ideas
- Intellectual Property
- Life Sciences
- Materials
- Tech Scout
- Unparalleled Data Quality
- Higher Quality Content
- 60% Fewer Hallucinations
Browse by: Latest US Patents, China's latest patents, Technical Efficacy Thesaurus, Application Domain, Technology Topic, Popular Technical Reports.
© 2025 PatSnap. All rights reserved.Legal|Privacy policy|Modern Slavery Act Transparency Statement|Sitemap|About US| Contact US: help@patsnap.com