Micro solder joint thermal migration test method
A test method and thermal migration technology, applied in the direction of thermal development of materials, can solve the problems of complex production, high cost, incomparability of thermal migration reliability data, etc., and achieve the effect of simple process and low cost
- Summary
- Abstract
- Description
- Claims
- Application Information
AI Technical Summary
Problems solved by technology
Method used
Image
Examples
example 1
[0023] Combining the following figure 1 , 2 , 3 specifically illustrate the implementation of the present invention.
[0024] 1. Cu pad preparation: the purity is greater than 99.99wt%, and the copper pad is made by wire cutting, and its size is 500μm×2mm×4mm;
[0025] 2. Clean the Cu pad in acetone for 5 minutes, then soak it in the prepared 30vol.% nitric acid aqueous solution for 10 minutes to remove oxides and pollutants on the surface of the Cu pad, and then put it in absolute ethanol Further ultrasonic cleaning, after cleaning and drying for later use;
[0026] 3. Adhere high-temperature-resistant double-sided adhesive on a 10mm×10mm×1.5mm printed circuit board, and place two Cu pads on it with a spacing of 130 μm, and ensure the parallelism of the Cu pads;
[0027] 4. Use a toothpick to fill the Sn0.3Ag0.7Cu solder paste between the two Cu pads, use a hot air reflow soldering machine (Comrade Technology, TN380C) for welding, and cool in the air to obtain Cu / Sn0.3Ag0....
example 2
[0029] Example 2: Combining the following figure 1 , 2 , 4 specifically describe the implementation of the present invention.
[0030] 1. Cu pad preparation: the purity is greater than 99.99wt%, and the copper pad is made by wire cutting, and its size is 500μm×2mm×4mm;
[0031] 2. Put the Cu pad in acetone for 5-10 minutes, then soak it in the prepared 30vol.% nitric acid aqueous solution for a few minutes to remove the oxides and pollutants on the surface of the Cu pad, and then put it into an anhydrous Further ultrasonic cleaning in ethanol, after cleaning, dry for later use;
[0032] 3. Adhere high-temperature-resistant double-sided adhesive on a 10mm×10mm×1.5mm printed circuit board, and place two Cu pads on it with a distance of 200 μm, and ensure the parallelism of the Cu pads;
[0033] 4. Use a toothpick to fill the Sn0.3Ag0.7Cu solder paste between the two Cu pads, use a hot air reflow soldering machine (Comrade Technology, TN380C) for welding, and cool in the air t...
PUM
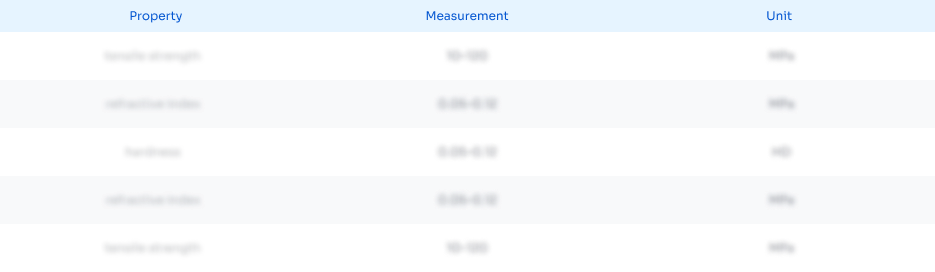
Abstract
Description
Claims
Application Information

- R&D
- Intellectual Property
- Life Sciences
- Materials
- Tech Scout
- Unparalleled Data Quality
- Higher Quality Content
- 60% Fewer Hallucinations
Browse by: Latest US Patents, China's latest patents, Technical Efficacy Thesaurus, Application Domain, Technology Topic, Popular Technical Reports.
© 2025 PatSnap. All rights reserved.Legal|Privacy policy|Modern Slavery Act Transparency Statement|Sitemap|About US| Contact US: help@patsnap.com