Preparation method of antifouling self-cleaning ceramic
A self-cleaning, ceramic technology, applied in the production of ceramic materials, clay products, applications, etc., can solve the problems of large porosity, difficulty in cleaning, ceramic surface pollution, etc., and achieve the effect of enhancing electronic ability and improving oxidation resistance
- Summary
- Abstract
- Description
- Claims
- Application Information
AI Technical Summary
Problems solved by technology
Method used
Image
Examples
example 1
[0023] In parts by weight, take 20 parts of kaolin, 25 parts of montmorillonite, 20 parts of bentonite and 60 parts of water to mix to obtain pottery clay slurry, and mix pottery clay slurry with egg white and activated sludge in a mass ratio of 10:1:1 After mixing, the fermentation substrate is obtained; put the fermentation substrate into the fermenter, seal the fermenter, and ferment for 10 days at 25°C. And mass fraction is that 30% sodium carboxymethyl cellulose solution is 50:1:1:8 to get ceramic base material after mixing by mass ratio; The ceramic base material that will obtain is injected in the stainless steel mould, with the pressure holding of 5MPa with sample press Press for 20 minutes to obtain a ceramic green body. Put the ceramic green body into an oven and dry it at a temperature of 105°C for 1 hour. After drying, a dry green body is obtained; The temperature was raised to 800°C at a rate of min, and the heat preservation and pre-fired for 1 hour. After the pr...
example 2
[0025] In parts by weight, take by weighing 23 parts of kaolin, 28 parts of montmorillonite, 25 parts of bentonite and 65 parts of water to mix to obtain pottery clay slurry, and mix pottery clay slurry with egg white and activated sludge in a mass ratio of 10:1:1 After mixing, the fermentation substrate is obtained; put the fermentation substrate into a fermenter, seal the fermenter, and ferment for 11 days at 30°C. And mass fraction is that 30% sodium carboxymethyl cellulose solution is 50:1:1:8 after mixing by mass ratio to get ceramic base material; Press for 23 minutes to obtain a ceramic green body. Put the ceramic green body into an oven and dry it at a temperature of 108°C for 1 hour. After drying, a dry green body is obtained; The temperature was raised to 850°C at a rate of min, and the heat preservation and pre-fired for 2 hours. After the pre-fired, the pre-fired ceramics were obtained. The tetrabutyl titanate and absolute ethanol were mixed at a mass ratio of 1:3 ...
example 3
[0027]In parts by weight, take 25 parts of kaolin, 30 parts of montmorillonite, 30 parts of bentonite and 70 parts of water to mix to obtain pottery clay slurry, and mix pottery clay slurry with egg white and activated sludge in a mass ratio of 10:1:1 After mixing, the fermentation substrate is obtained; put the fermentation substrate into a fermenter, seal the fermenter, and ferment for 12 days at 35°C. And mass fraction is that 30% sodium carboxymethyl cellulose solution mixes by mass ratio 50:1:1:8 to get ceramic base material; The ceramic base material that will obtain is injected in the stainless steel mould, with the pressure holding of 8MPa with sample press Press for 30 minutes to obtain a ceramic green body. Put the ceramic green body into an oven first, and dry it at a temperature of 110°C for 2 hours. After drying, a dry green body is obtained; The temperature was raised to 900°C at a rate of min, and the heat preservation and pre-fired for 2 hours. After the pre-fi...
PUM
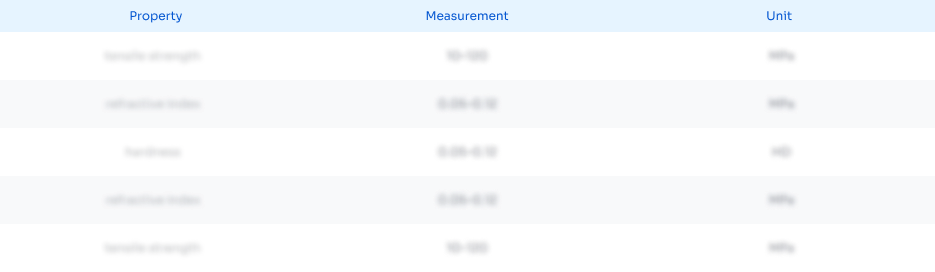
Abstract
Description
Claims
Application Information

- R&D
- Intellectual Property
- Life Sciences
- Materials
- Tech Scout
- Unparalleled Data Quality
- Higher Quality Content
- 60% Fewer Hallucinations
Browse by: Latest US Patents, China's latest patents, Technical Efficacy Thesaurus, Application Domain, Technology Topic, Popular Technical Reports.
© 2025 PatSnap. All rights reserved.Legal|Privacy policy|Modern Slavery Act Transparency Statement|Sitemap|About US| Contact US: help@patsnap.com