Method for preparing ethanol by ethyl acetate hydrogenation
A technology for producing ethyl acetate and ethanol, which is applied in chemical instruments and methods, preparation of hydroxyl compounds, preparation of organic compounds, etc., can solve the problems of high price, low space velocity, high reaction temperature and pressure of ethanol, and achieve low price, The effect of good activity stability and long operation time
- Summary
- Abstract
- Description
- Claims
- Application Information
AI Technical Summary
Problems solved by technology
Method used
Image
Examples
Embodiment 1
[0022] Mix and stir a certain amount of ferric nitrate, tin tetrachloride and deionized water evenly to obtain an impregnation solution containing Co‐Sn; add a certain amount of α‐Al to the above impregnation solution 2 o 3 The carrier was aged at room temperature for 24 hours, then dried at 80°C for 4 hours, and calcined at 700°C for 4 hours to obtain a catalyst precursor;
[0023] The catalyst precursor is reduced, the reduction temperature is 400°C, the reduction time is 10h, the hydrogen content in the hydrogen-containing atmosphere is 15% by volume, and the volume space velocity of the hydrogen-containing atmosphere is 2000h ‐1 , to obtain catalyst I. By adjusting the amount of active components and supports, the composition of catalyst I is: Co content 10.5% by weight, Sn content 5.6% by weight, α-Al 2 o 3 The content of 83.9% by weight.
Embodiment 2
[0025] Mix and stir a certain amount of ferric nitrate, tin tetrachloride and deionized water evenly to obtain an impregnation solution containing Co‐Sn; add a certain amount of γ‐Al to the above impregnation solution 2 o 3 The carrier was aged at room temperature for 24 hours, then dried at 80°C for 4 hours, and calcined at 700°C for 4 hours to obtain a catalyst precursor;
[0026] The catalyst precursor is reduced, the reduction temperature is 400°C, the reduction time is 10h, the hydrogen content in the hydrogen-containing atmosphere is 15% by volume, and the volume space velocity of the hydrogen-containing atmosphere is 2000h ‐1 , to obtain Catalyst II. By adjusting the amount of active components and supports, the composition of Catalyst II is: Co content 6.6% by weight, Sn content 12.1% by weight, γ‐Al 2 o 3 The content of 81.1% by weight.
Embodiment 3
[0028] Mix and stir a certain amount of ferric nitrate, tin tetrachloride and deionized water evenly to obtain an impregnation solution containing Co‐Sn; add a certain amount of γ‐Al to the above impregnation solution 2 o 3 The carrier was aged at room temperature for 24 hours, then dried at 80°C for 4 hours, and calcined at 700°C for 4 hours to obtain a catalyst precursor;
[0029] The catalyst precursor is reduced, the reduction temperature is 400°C, the reduction time is 10h, the hydrogen content in the hydrogen-containing atmosphere is 15% by volume, and the volume space velocity of the hydrogen-containing atmosphere is 2000h ‐1 , to obtain catalyst III. By adjusting the amount of active components and supports, the composition of catalyst III is: Co content 8.6% by weight, Sn content 12.1% by weight, γ‐Al 2 o 3 The content of 79.3% by weight.
PUM
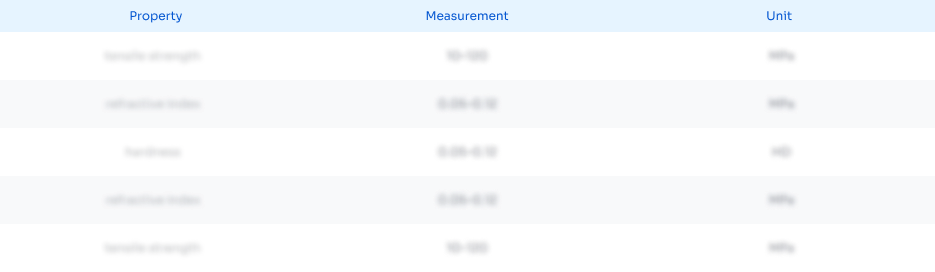
Abstract
Description
Claims
Application Information

- Generate Ideas
- Intellectual Property
- Life Sciences
- Materials
- Tech Scout
- Unparalleled Data Quality
- Higher Quality Content
- 60% Fewer Hallucinations
Browse by: Latest US Patents, China's latest patents, Technical Efficacy Thesaurus, Application Domain, Technology Topic, Popular Technical Reports.
© 2025 PatSnap. All rights reserved.Legal|Privacy policy|Modern Slavery Act Transparency Statement|Sitemap|About US| Contact US: help@patsnap.com