Method for preparing white carbon black by cutting zirconium silicon slag
A technology of zirconium-silicon slag and white carbon black, which is applied in the field of white carbon black preparation, can solve the problems of ineffective removal of impurity ions and low activity of zirconium-silicon slag, and achieve the effects of reducing stability, improving utilization rate, and increasing specific surface area
- Summary
- Abstract
- Description
- Claims
- Application Information
AI Technical Summary
Problems solved by technology
Method used
Image
Examples
Embodiment 1
[0030] A method for preparing white carbon black by cutting zirconium silicon slag, comprising the following steps:
[0031] 1) Activate the zirconium-silicon slag, place the zirconium-silicon slag in a rotary dryer, dry for 1 hour, the drying temperature is 130°C, and cool down to 20°C;
[0032] 2) ultrasonically crush the zirconium-silicon slag, and heat the zirconium-silicon slag at 150°C to obtain activated zirconium-silicon slag;
[0033] 3) After activating the zirconium silicon slag, add 3 times the solid volume of water, dispersant NH with a solid mass fraction of 1% 4 CL, scrub and scrub 3 times repeatedly to fully melt the zirconium-silicon slag;
[0034] 4) Add NaOH to the silica sol, adjust the pH to 9, and add AI 2 (SO 4 ) 3 Raise the temperature to 80°C, then add polyethylene glycol and stir for 40 minutes, then let stand for 30 minutes to obtain hydrated silica;
[0035] 5) The hydrated silica prepared in step 4) was calcined at 630° C. for 20 minutes, and ...
Embodiment 2
[0037] A method for preparing white carbon black by cutting zirconium silicon slag, comprising the following steps:
[0038] 1) Activate the zirconium-silicon slag, place the zirconium-silicon slag in a rotary dryer, dry for 2 hours, the drying temperature is 150°C, and cool down to 30°C;
[0039] 2) ultrasonically crush the zirconium-silicon slag, and heat the zirconium-silicon slag at 150°C to obtain activated zirconium-silicon slag;
[0040] 3) After activating the zirconium silicon slag, add 4 times the solid volume of water, dispersant NH with a solid mass fraction of 1% 4 CL, scrub and scrub 4 times repeatedly to fully melt the zirconium-silicon slag;
[0041] 4) Add NaOH to the silica sol, adjust the pH to 9, and add AI 2 (SO 4 ) 3 Raise the temperature to 80°C, then add polyethylene glycol and stir for 40 minutes, then let stand for 30 minutes to obtain hydrated silica;
[0042] 5) The hydrated silica prepared in step 4) was calcined at 660° C. for 20 minutes, and...
Embodiment 3
[0044] A method for preparing white carbon black by cutting zirconium silicon slag, comprising the following steps:
[0045]1) Activate the zirconium-silicon slag, place the zirconium-silicon slag in a rotary dryer, and dry it for 1.5 hours at a drying temperature of 130°C, then cool it down to 25°C;
[0046] 2) ultrasonically crush the zirconium-silicon slag, and heat the zirconium-silicon slag at 150°C to obtain activated zirconium-silicon slag;
[0047] 3) After activating the zirconium silicon slag, add 4 times the solid volume of water, dispersant NH with a solid mass fraction of 1% 4 CL, scrub repeatedly 3-4 times to fully melt the zirconium and silicon slag;
[0048] 4) Add NaOH to the silica sol, adjust the pH to 9, and add AI 2 (SO 4 ) 3 Raise the temperature to 80°C, then add polyethylene glycol and stir for 40 minutes, then let stand for 30 minutes to obtain hydrated silica;
[0049] 5) The hydrated silica prepared in step 4) was calcined at 3500° C. for 20 min...
PUM
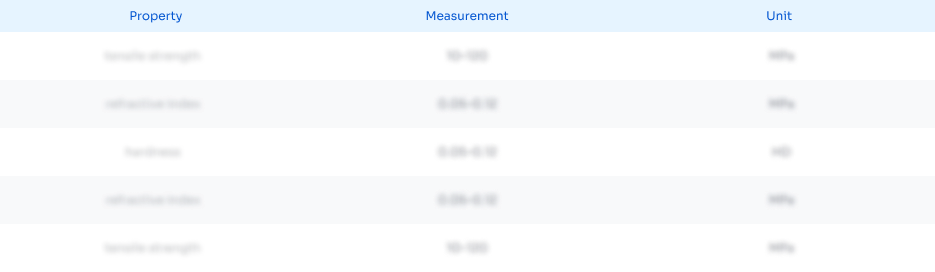
Abstract
Description
Claims
Application Information

- R&D Engineer
- R&D Manager
- IP Professional
- Industry Leading Data Capabilities
- Powerful AI technology
- Patent DNA Extraction
Browse by: Latest US Patents, China's latest patents, Technical Efficacy Thesaurus, Application Domain, Technology Topic, Popular Technical Reports.
© 2024 PatSnap. All rights reserved.Legal|Privacy policy|Modern Slavery Act Transparency Statement|Sitemap|About US| Contact US: help@patsnap.com