Preparation method of antiskid glazed tile
A technology for glazed tiles and preparation steps, applied in the field of preparation of anti-slip glazed tiles, can solve the problem that the anti-slip performance cannot be further improved, and achieve the effects of improving the anti-slip performance, increasing the friction force, and improving the roughness
- Summary
- Abstract
- Description
- Claims
- Application Information
AI Technical Summary
Problems solved by technology
Method used
Examples
example 1
[0023] In parts by weight, iron ore slag, copper slag, and mica slag are placed in a ball mill for ball milling, and a 120-mesh sieve is passed to obtain a slag mixture; in parts by weight, 10 parts of Suzhou soil, 8 parts of talcum powder, 60 parts of wollastonite and 30 parts of Kuancheng soil are ball milled in a ball mill and passed through a 180-mesh sieve to obtain a mixed powder; in parts by weight, 30 parts of straw, 30 parts of cotton stalk and 30 parts of walnut shell are placed in a pulverizer Grinding in medium and passing through a 120-mesh sieve to obtain mixed slag; in parts by weight, 20 parts of mixed slag, 5 parts of secondary sedimentation tank sludge, and 40 parts of water are placed in a fermentation kettle at a temperature of 35 ° C and a rotation speed of Under the condition of 200r / min, ferment for 8 days to obtain the fermented mixed solution; in parts by weight, 30 parts of mixed powder, 20 parts of fermented mixed solution, and 60 parts of water are p...
example 2
[0025] In parts by weight, 10 parts of Suzhou soil, 8 parts of talcum powder, 60 parts of wollastonite, and 30 parts of Kuancheng soil are placed in a ball mill for ball milling, and a 180-mesh sieve is passed to obtain a mixed powder; 30 parts of stalks, 30 parts of cotton stalks, 30 parts of walnut shells are placed in a pulverizer and pulverized, and passed through a 120-mesh sieve to obtain mixed slag; in parts by weight, 20 parts of mixed slag, 5 parts of secondary sedimentation tank sludge, 40 parts of water are placed in a fermentation tank, and fermented for 8 days at a temperature of 35°C and a rotating speed of 200r / min to obtain a fermentation mixture; in parts by weight, 30 parts of mixed powder and 20 parts of fermentation mixture, Put 60 parts of water in the mixer, stir and mix for 50 minutes at a speed of 200r / min to obtain a mixed slurry, then place the mixed slurry in a compression molding machine, and mold it under a pressure of 5MPa. The adobe is obtained, ...
example 3
[0027] In parts by weight, iron ore slag, copper slag, and mica slag are placed in a ball mill for ball milling, and a 120-mesh sieve is passed to obtain a slag mixture; in parts by weight, 10 parts of Suzhou soil, 8 parts of talcum powder, 60 parts of wollastonite and 30 parts of Kuancheng soil are ball milled in a ball mill and passed through a 180-mesh sieve to obtain a mixed powder; in parts by weight, 30 parts of mixed powder and 60 parts of water are placed in a mixer, Under the condition of 200r / min, stir and mix for 50min to obtain a mixed slurry, then place the mixed slurry in a compression molding machine, and mold it under a pressure of 5MPa to obtain a brick, then place the brick in an oven, Under the condition of 110°C, dry to constant weight to obtain dry bricks; in parts by weight, 5 parts of slag mixture, 40 parts of clay, 10 parts of bacterial cellulose, 10 parts of bauxite, 5 parts of phospholipid, 60 parts of Put a portion of water in a mixer, and stir and m...
PUM
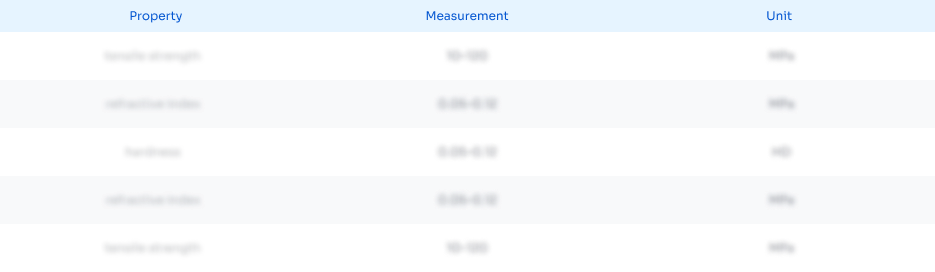
Abstract
Description
Claims
Application Information

- R&D Engineer
- R&D Manager
- IP Professional
- Industry Leading Data Capabilities
- Powerful AI technology
- Patent DNA Extraction
Browse by: Latest US Patents, China's latest patents, Technical Efficacy Thesaurus, Application Domain, Technology Topic, Popular Technical Reports.
© 2024 PatSnap. All rights reserved.Legal|Privacy policy|Modern Slavery Act Transparency Statement|Sitemap|About US| Contact US: help@patsnap.com