Method and device for measuring calorimetry of non-isothermal reaction process
A technology of reaction process and measurement method, applied in the direction of material thermal development, etc., can solve the problem of lack of non-isothermal reaction process calorimetric methods
- Summary
- Abstract
- Description
- Claims
- Application Information
AI Technical Summary
Problems solved by technology
Method used
Image
Examples
Embodiment 1
[0074] Such as figure 1 As shown, the present invention includes a control system and a reaction system module, wherein the reaction system module includes a reactor 1, a feeding system 4, a distillation system 5, a heater 9, a temperature control module, and a pressure monitoring module. The reactor 1 is equipped with a stirring system 6, the feeding system 4 is connected to the feed port of the reactor 1 through a pipeline, and the distillation and back distillation system 5 is connected to the discharge port of the reactor 1 through a pipeline. The back distillation system 5 is controlled by the control system to start and stop. One end of the heater 9 extends into the reactor 1 and heats the interior of the reactor 1, and the heater 9 transmits to the control system through the temperature control module. A signal is sent to adjust the heating temperature, and a pressure monitoring module is provided in the reactor 1.
[0075] Such as figure 1 As shown, the control system i...
Embodiment 2
[0090] Acetic anhydride hydrolysis test.
[0091] According to the above device, water was added to the reactor. After the addition, the feed port of the reactor was sealed, and then acetic anhydride was added dropwise through the liquid feeding system. The molar ratio of acetic anhydride to water was 1:22.7. Acetic anhydride was added dropwise at 30°C. , After 50min of dripping, the reaction is kept for 10min after the dropping; the temperature is raised to 40℃ at a rate of 1℃ / min, and the reaction is kept for 1h; the temperature is raised to 50℃ at a rate of 1℃ / min, and the reaction is kept for 1h, and the reaction is over.
[0092] experiment procedure:
[0093] According to the actual feeding situation, set the control program, drip temperature 30℃, stir 300rpm, run heating, calibration, dripping materials, heat preservation, heat preservation, heat preservation, heat preservation, heat preservation, calibration procedures in sequence; The material system is cleaned; the experim...
Embodiment 3
[0097] 3-cyanopyridine and phosphorus oxychloride are chlorinated to prepare 2-chloro-3-cyanopyridine.
[0098] According to the above device records, solid 3-cyanopyridine, dimethylformamide and xylene were added to the reactor. After the addition, the reactor inlet was sealed, and then phosphorus oxychloride was added dropwise through the liquid feeding system. The molar ratio of cyanopyridine (104), phosphorus oxychloride (153.3), dimethylformamide (73.1) and xylene (106.2) is 1:1.3:1.8:2. Phosphorus oxychloride is added dropwise at 90°C, After 1h of dripping, the reaction is kept for 2h after dripping; the temperature is raised to 100°C at a rate of 0.5°C / min, and the reaction is kept for 3h; the temperature is raised to 120°C at a rate of 1°C / min, and the reaction is kept for 2h, and the reaction is over.
[0099] experiment procedure:
[0100] According to the actual feeding situation, set the control program, drip temperature 90℃, stir 300rpm, run heating, calibration, drippi...
PUM
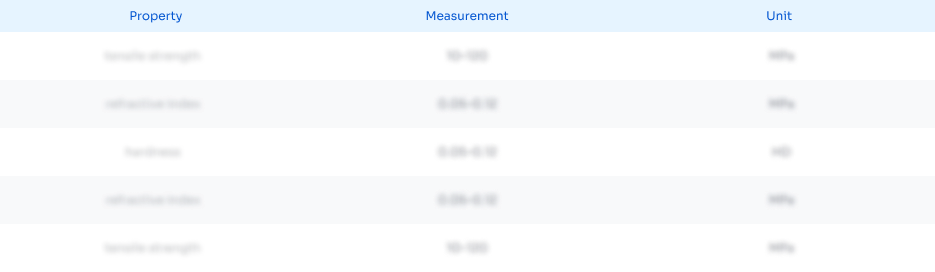
Abstract
Description
Claims
Application Information

- R&D
- Intellectual Property
- Life Sciences
- Materials
- Tech Scout
- Unparalleled Data Quality
- Higher Quality Content
- 60% Fewer Hallucinations
Browse by: Latest US Patents, China's latest patents, Technical Efficacy Thesaurus, Application Domain, Technology Topic, Popular Technical Reports.
© 2025 PatSnap. All rights reserved.Legal|Privacy policy|Modern Slavery Act Transparency Statement|Sitemap|About US| Contact US: help@patsnap.com