Preparation method of composite coating capable of improving high-temperature anti-oxidization performance of titanium alloy
A high-temperature anti-oxidation and composite coating technology, which is applied in the coating process and coating of metal materials, can solve the problems of poor performance of MoSi2
- Summary
- Abstract
- Description
- Claims
- Application Information
AI Technical Summary
Problems solved by technology
Method used
Image
Examples
Embodiment 1
[0042] (1) Put the configured composite powder into a ball mill (QM-3SP04) for 12 hours to obtain an alloy powder mixture and dry it;
[0043] (2) Using methyl cellulose solution as the binder, the mixed alloy powder of coating 1 is pre-placed on the surface of the titanium alloy TC4 substrate with a thickness of about 1.5 mm, and the temperature is maintained in a drying oven at 120°C for 2 hours;
[0044] (3) A semiconductor laser (DLS-980.10-3000C) with an output power of 1kW is used to scan the surface of the preset alloy powder, the laser beam output rectangular spot is 6mm×6mm, and the scanning speed is 4mm / s;
[0045] (4) Using single-channel laser scanning technology to prepare high-temperature anti-oxidation composite coating.
Embodiment 2
[0047] (1) Put the configured composite powder into a ball mill (QM-3SP04) for 12 hours to obtain an alloy powder mixture and dry it;
[0048] (2) Using methyl cellulose solution as the adhesive, pre-place the mixed alloy powder of coating 2 on the surface of the titanium alloy TC4 substrate with a thickness of about 1.5 mm, and heat it in a drying oven at 120°C for 2 hours;
[0049] (3) A semiconductor laser (DLS-980.10-3000C) with an output power of 1.5kW is used to scan the surface of the preset alloy powder, the laser beam output spot is 6mm×6mm, and the scanning speed is 4mm / s;
[0050] (4) Using single-channel laser scanning technology to prepare high-temperature anti-oxidation composite coating.
Embodiment 3
[0052] (1) Put the configured composite powder into a ball mill (QM-3SP04) for 12 hours to obtain an alloy powder mixture and dry it;
[0053] (2) Using methyl cellulose solution as the binder, pre-place the mixed alloy powder of coating 3 on the surface of the titanium alloy TC4 substrate with a thickness of about 1.5 mm, and heat it in a drying oven at 120°C for 2 hours;
[0054] (3) A semiconductor laser (DLS-980.10-3000C) with an output power of 1.8kW is used to scan the surface of the prefabricated powder, and its rectangular spot is 6mm×6mm. The laser scanning speed is 4mm / s;
[0055] (4) Using single-channel laser scanning technology to prepare high-temperature anti-oxidation composite coating.
PUM
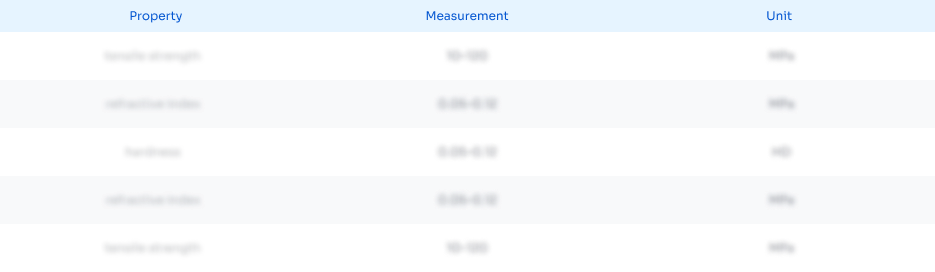
Abstract
Description
Claims
Application Information

- Generate Ideas
- Intellectual Property
- Life Sciences
- Materials
- Tech Scout
- Unparalleled Data Quality
- Higher Quality Content
- 60% Fewer Hallucinations
Browse by: Latest US Patents, China's latest patents, Technical Efficacy Thesaurus, Application Domain, Technology Topic, Popular Technical Reports.
© 2025 PatSnap. All rights reserved.Legal|Privacy policy|Modern Slavery Act Transparency Statement|Sitemap|About US| Contact US: help@patsnap.com