Composite leather and manufacturing method thereof
A manufacturing method and leather technology, applied in textiles, papermaking, fiber processing, etc., can solve the problems of limited improvement of air permeability and mechanical properties, and achieve the effects of improved wearing experience, good waterproof performance, good air permeability and hand feeling
- Summary
- Abstract
- Description
- Claims
- Application Information
AI Technical Summary
Problems solved by technology
Method used
Examples
Embodiment 1
[0040] A kind of compound leather and manufacture method thereof, comprises the following steps:
[0041] (1) Prepare the base cloth, impregnate the base cloth with an inorganic mixture, squeeze the liquid and then dry it;
[0042] (2) To prepare slurry, add 8 parts of foaming agent to 80 parts of water-based polyurethane, and mix evenly to obtain water-based polyurethane slurry;
[0043] (3) Squeegee-coating slurry, scrape-coating the water-based polyurethane slurry on the base cloth, drying and cooling to obtain the water-based polyurethane leather bass;
[0044](4) Surface treatment: use a finishing agent to carry out surface finishing treatment on the water-based polyurethane leather bass to obtain composite leather. In the step of preparing the base cloth, the inorganic mixed solution includes 1 mass part of nano-calcium carbonate, 1 mass part of nano-zirconia, 2 mass parts of nano-titanium dioxide, 2 mass parts of nano-zinc oxide, and 100 mass parts of deionized water ...
Embodiment 2
[0048] The difference between Example 2 and Example 1 is that in the step of preparing the base cloth, the base cloth is soaked in the inorganic mixed liquid, and the amount of impregnation is 50% of the weight of the base cloth, and the amount of impregnation after liquid rolling is based on 30% of the weight of the cloth, and the base cloth after the squeezed liquid is dried at 100°C;
[0049] In the described scraping slurry step, the scraping amount of the slurry is 260g / m 2 , the drying temperature is 80°C;
[0050] In the described surface treatment step, the finishing agent is rolled onto the water-based polyurethane leather bass, and the roll coating amount is 20g / m 2 , the drying temperature is 80°C.
Embodiment 3
[0052] The difference between Example 3 and Example 1 is that in the step of preparing the base cloth, the base cloth is dipped in the inorganic mixture, and the amount of impregnation is 70% of the weight of the base cloth. 50% of the weight of the cloth, and the base cloth after the squeezed liquid is dried at 150°C;
[0053] In the described scraping slurry step, the scraping amount of the slurry is 500g / m 2 , the drying temperature is 150°C;
[0054] In the surface treatment step, the finishing agent is rolled onto the water-based polyurethane leather bass, and the amount of roll coating is 40g / m 2 , the drying temperature is 150°C.
PUM
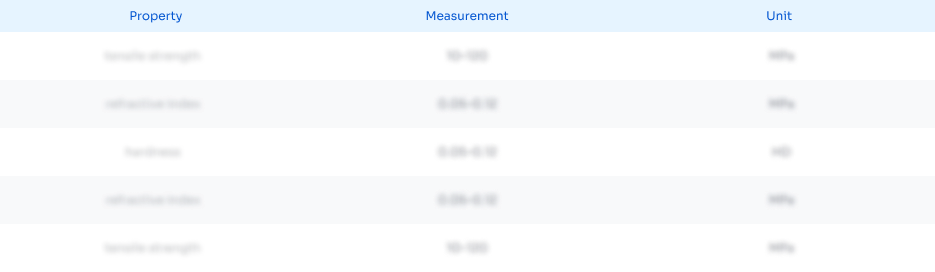
Abstract
Description
Claims
Application Information

- R&D
- Intellectual Property
- Life Sciences
- Materials
- Tech Scout
- Unparalleled Data Quality
- Higher Quality Content
- 60% Fewer Hallucinations
Browse by: Latest US Patents, China's latest patents, Technical Efficacy Thesaurus, Application Domain, Technology Topic, Popular Technical Reports.
© 2025 PatSnap. All rights reserved.Legal|Privacy policy|Modern Slavery Act Transparency Statement|Sitemap|About US| Contact US: help@patsnap.com