Method for reducing bubbles of continuous casting primary blank
A continuous casting and bubble technology is applied in the field of reducing the bubbles of the continuous casting head billet, which can solve the problems of increased production cost, long tundish, uneven baking, etc., and achieve the effects of improving the quality of the casting billet, reducing the bubbles, and reducing the production cost.
- Summary
- Abstract
- Description
- Claims
- Application Information
AI Technical Summary
Problems solved by technology
Method used
Examples
Embodiment 1
[0010] Embodiment 1: The method for reducing air bubbles in the continuous casting billet adopts the following specific processes.
[0011] (1) Taking the steel HPB300 for wire rod as an example, before the first furnace of continuous casting starts pouring, after the tundish is baked and opened to the working position, silicon-calcium powder is added to the nozzle of the tundish. See Table 1 for the baking temperature of the tundish before continuous casting, the temperature of molten steel and the amount of silicon-calcium powder added to the tundish.
[0012] Table 1: Continuous casting casting parameters
[0013] Tundish baking temperature / ℃
Molten steel temperature / ℃
Molten steel weight / ton
Addition amount of CaSi powder / kg
1131
1607
125
150
[0014] The CaSi powder was sampled and tested, and the test results are shown in Table 2.
[0015] Table 2: CaSi powder main component content (wt)
[0016] ingredient name
Si...
Embodiment 2
[0020] Embodiment 2: The method for reducing air bubbles in the continuous casting billet adopts the following specific processes.
[0021] (1) Taking the steel HPB300 for wire rod as an example, see Table 4 for the baking temperature of the tundish before continuous casting, the temperature of molten steel and the amount of silicon-calcium powder added to the tundish.
[0022] Table 4: Continuous casting casting parameters
[0023] Tundish baking temperature / ℃
Molten steel temperature / ℃
Molten steel weight / ton
Addition amount of CaSi powder / kg
1131
1603
125
200
[0024] The CaSi powder was sampled and tested, and the test results are shown in Table 5.
[0025] Table 5: CaSi powder main component content (wt)
[0026] ingredient name
Si
Ca
Al
C
P
S
Ingredient content / %
55
29
2.3
0.8
0.05
0.04
[0027] (2) The size of the small slab crystallizer, the length of the cast slab, t...
Embodiment 3
[0030] Embodiment 3: The method for reducing air bubbles in the continuous casting billet adopts the following specific processes.
[0031] (1) Taking steel 81MnCrV for wire as an example, see Table 7 for the baking temperature of the tundish before continuous casting, the temperature of molten steel and the amount of silicon-calcium powder added to the tundish.
[0032] Table 7: Continuous casting start-up parameters
[0033] Tundish baking temperature / ℃
Molten steel temperature / ℃
Molten steel weight / ton
Addition amount of CaSi powder / kg
1120
1550
125
180
[0034] The CaSi powder was sampled and tested, and the test results are shown in Table 8.
[0035] Table 8: CaSi powder main component content (wt)
[0036] ingredient name
Si
Ca
Al
C
P
S
Ingredient content / %
59
28
1.9
0.72
0.053
0.035
[0037] (2) The size of the small slab crystallizer, the length of the slab, the count...
PUM
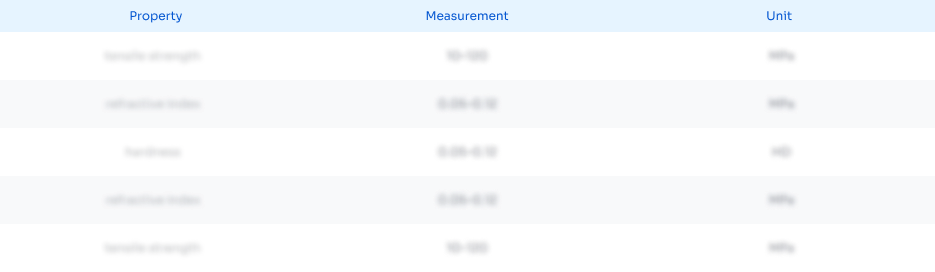
Abstract
Description
Claims
Application Information

- R&D
- Intellectual Property
- Life Sciences
- Materials
- Tech Scout
- Unparalleled Data Quality
- Higher Quality Content
- 60% Fewer Hallucinations
Browse by: Latest US Patents, China's latest patents, Technical Efficacy Thesaurus, Application Domain, Technology Topic, Popular Technical Reports.
© 2025 PatSnap. All rights reserved.Legal|Privacy policy|Modern Slavery Act Transparency Statement|Sitemap|About US| Contact US: help@patsnap.com