The preparation method of ethyl 2-oxo-3-piperidinecarboxylate
A technology of ethyl piperidinecarboxylate and diethyl malonate, which is applied in the field of preparation of ethyl 2-oxo-3-piperidinecarboxylate, can solve the problems of low yield, and achieve easy-to-obtain raw materials and simple operation Effect
- Summary
- Abstract
- Description
- Claims
- Application Information
AI Technical Summary
Problems solved by technology
Method used
Image
Examples
Embodiment 1
[0025] 1000mL dry four-necked reaction flask, equipped with mechanical stirring, thermometer, dropping funnel, and reflux condenser. Add 560 g (3.5 mol) of diethyl malonate, 0.6 g (solid powder) of sodium tert-butoxide as a basic catalyst, and 70 g (1.3 mol) of acrylonitrile into the dropping funnel. Add acrylonitrile dropwise to the reaction bottle under stirring, the reaction exotherms, control the reaction temperature at 30-32°C with a water bath, and complete the addition in 4-5 hours. Then the reaction was stirred at the same temperature for 1 hour.
[0026] Transfer the feed liquid into a 1000mL vacuum short column rectification device, remove the raw material diethyl malonate at a vacuum of 18-20 mmHg, then increase the vacuum to 0.6-0.8 mmHg, and distill the distillate at a temperature of 106-206 mmHg. The positive fraction at 110°C was 227.6 g in total, the GC content of the intermediate 2-cyanoethyldiethylmalonate was 98.6%, and the reaction yield was 80.9% (calcula...
Embodiment 2
[0030] The 1000 liter glass-lined reactor was washed and dried in N 2 Under protection, 620 kg (3.87 kmol) of diethyl malonate and 0.9 kg of solid powder of potassium tert-butoxide were added. 72kg of acrylonitrile is introduced into the overhead tank. (1.35kmol) Start the stirring of the reactor, and drop acrylonitrile into the reactor within 5 hours when the internal temperature is lower than 35°C. After the addition of acrylonitrile, the reaction was carried out at 32°C for 1 hour.
[0031] The reaction feed liquid is transferred from the reactor to the short-column rectification tower of the 1000-liter tower tank. Start the vacuum system to make the vacuum degree reach 20-25mmHg, turn on the cooling water circulation of the condenser at the top of the tower, introduce steam into the reboiler of the tower to heat, and distill out the solvent diethyl malonate at a reflux ratio of 1:1. When the diethyl malonate is completely evaporated, turn on the multi-stage Roots vacuum...
Embodiment 3~8
[0039] Embodiment 3~8 all repeats the operation of embodiment 2, but the diethyl malonate of raw material diethyl malonate is reclaimed the diethyl malonate of redistilling and adds fresh substance again to reach requirement feeding amount; After 0.5kg, put it into the next kettle for reaction; all the recrystallization operations of the product use fresh solvents.
[0040] The reaction results are as follows:
[0041]
[0042]
PUM
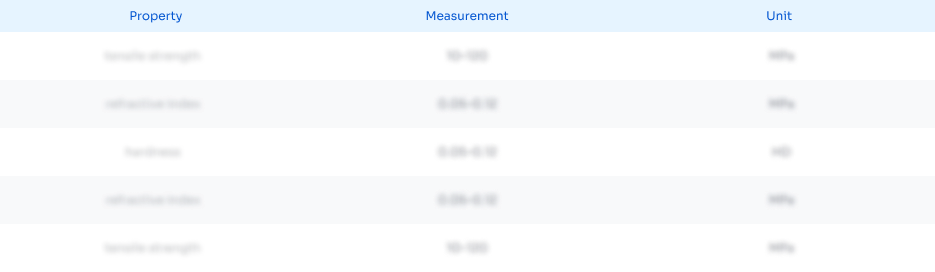
Abstract
Description
Claims
Application Information

- Generate Ideas
- Intellectual Property
- Life Sciences
- Materials
- Tech Scout
- Unparalleled Data Quality
- Higher Quality Content
- 60% Fewer Hallucinations
Browse by: Latest US Patents, China's latest patents, Technical Efficacy Thesaurus, Application Domain, Technology Topic, Popular Technical Reports.
© 2025 PatSnap. All rights reserved.Legal|Privacy policy|Modern Slavery Act Transparency Statement|Sitemap|About US| Contact US: help@patsnap.com