Solvent-free polyurethane resin and application thereof to waterborne/non-solvent polyurethane synthetic leather with high peeling strength
A solvent-free polyurethane and solvent-free technology, which is applied in the field of synthetic leather manufacturing, can solve the problem of poor bonding strength between water-based polyurethane surface layer and solvent-free polyurethane foam layer, low water-based/solvent-free peel strength, and inability to apply peel strength to shoe leather To improve the poor peel strength, cross-link density between polymers, and excellent hydrolysis aging resistance
- Summary
- Abstract
- Description
- Claims
- Application Information
AI Technical Summary
Problems solved by technology
Method used
Image
Examples
Embodiment 1
[0036] (1) Preparation of water-based surface layer slurry and solvent-free foam layer slurry
[0037] a) Preparation of water-based surface layer slurry (parts by weight)
[0038] The preparation process of double-bond-terminated waterborne polyurethane resin is as follows: first add 20 parts by weight of isophorone diisocyanate, 100 parts of polyhexamethylene adipate diol and 1 part of dibutyltin dilaurate catalyst in the reactor, 75 ℃ for 1~2h, add 10 parts of dimethylolpropionic acid, heat up to 85℃ and react for 2h; then cool down to 50℃, add 4 parts of pentaerythritol triacrylate and 2 parts of p-hydroxyanisole inhibitor, 60℃ React for 3 hours; finally add triethylamine at 40°C and stir for 0.5 hours, then add 250 parts of deionized water and stir for 1-2 hours to obtain a double-bond-terminated water-based polyurethane emulsion.
[0039] 100 parts of double bond-terminated water-based polyurethane, 2 parts of photoinitiator (Darocurl173), 10 parts of water-based color ...
Embodiment 2
[0048] (1) Preparation of water-based surface layer slurry and solvent-free foam layer slurry
[0049] a) Preparation of water-based surface layer slurry (parts by weight)
[0050] The preparation process of the double-bond-terminated water-based polyurethane resin is as follows: first, 25 parts of isophorone diisocyanate, 90 parts of polyhexamethylene adipate diol and 1.5 parts of dibutyltin dilaurate catalyst, pass into N 2 After reacting at 90°C for 1.5h, cool down to 75°C, add 8 parts of dimethylol propionic acid, raise the temperature to 95°C for 2 hours; then cool down to 60°C, add measured 5 parts of pentaerythritol triacrylate and 1 part of p-hydroxybenzene Methyl ether polymerization inhibitor, react at 65°C for 4h; finally add triethylamine at 45°C and stir for 0.5h, then add 250 parts of deionized water and stir at high speed for 1.5h to obtain double bond-terminated water-based polyurethane emulsion.
[0051] 100 parts of double bond-terminated water-based polyur...
Embodiment 3
[0060] (1) Preparation of water-based surface layer slurry and solvent-free foam layer slurry
[0061] a) Preparation of water-based surface layer slurry (parts by weight)
[0062] First, add 30 parts of isophorone diisocyanate, 80 parts of polyhexamethylene adipate diol and 2 parts of dibutyltin dilaurate catalyst into a four-necked flask equipped with a thermometer and an electric stirrer, and feed N2, 88 After reacting at ℃ for 1 hour, cool down to 75℃, add 6 parts of dimethylol propionic acid, raise the temperature to 88℃ and react for 2 hours; Polymerizing agent, react at 65°C for 4h; finally add triethylamine at 45°C and stir for 0.5h, then add 300 parts of deionized water and stir at high speed for 1h to obtain a double-bond-terminated water-based polyurethane emulsion.
[0063] 100 parts of double bond-terminated water-based polyurethane, 5 parts of photoinitiator (Darocurl173), 1 part of water-based color paste, 5 parts of thickener (LW44), 2 parts of defoamer (BK-01...
PUM
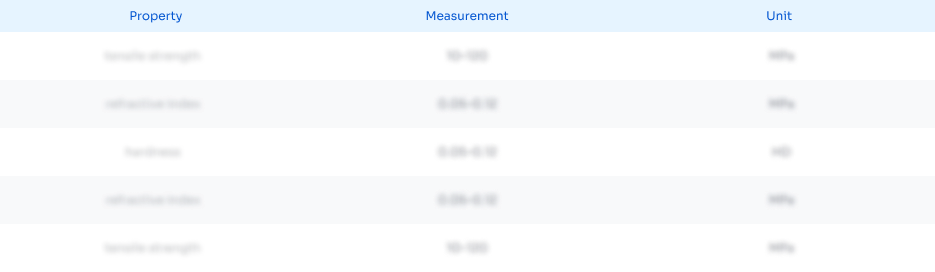
Abstract
Description
Claims
Application Information

- Generate Ideas
- Intellectual Property
- Life Sciences
- Materials
- Tech Scout
- Unparalleled Data Quality
- Higher Quality Content
- 60% Fewer Hallucinations
Browse by: Latest US Patents, China's latest patents, Technical Efficacy Thesaurus, Application Domain, Technology Topic, Popular Technical Reports.
© 2025 PatSnap. All rights reserved.Legal|Privacy policy|Modern Slavery Act Transparency Statement|Sitemap|About US| Contact US: help@patsnap.com