Method for separating lignin from bagasse, and special equipment thereof
A technology of separation equipment and special equipment, which is applied in the field of waste recycling of agricultural products, can solve the problems of high energy consumption, organic wastewater, and high equipment requirements, and achieve the effects of low energy consumption, increased crushing speed, and high energy-flux density
- Summary
- Abstract
- Description
- Claims
- Application Information
AI Technical Summary
Problems solved by technology
Method used
Image
Examples
Embodiment 1
[0041] The method for separating lignin from bagasse, concrete operations are as follows:
[0042] (1) Bagasse pretreatment: first put the bagasse into a 90°C water bath for 30 minutes, and then dry the bagasse treated in the water bath by air blast to make the natural moisture content of the bagasse < 8%;
[0043] (2) Bagasse steam explosion pulping: Put the bagasse processed by blast drying in step (1) into the steam explosion pulping equipment, first inject water vapor to pressurize to 1.3MPa, keep the pressure for 10min, and then Increase the pressure to 1.5MPa, immediately open the valve to release the pressure, blast the bagasse into a cotton-like bagasse slurry, and carry out blast drying treatment on the obtained bagasse slurry again, so that the natural moisture of the bagasse slurry is <4%. Then the bagasse slurry is pulverized to 40 mesh to obtain bagasse slurry powder;
[0044] (3) Ultrasonic separation: Add the bagasse slurry powder obtained in step (2) into dist...
Embodiment 2
[0051] The method for separating lignin from bagasse, concrete operations are as follows:
[0052] (1) Bagasse pretreatment: first put the bagasse into a 100°C water bath for cleaning for 20 minutes, and then dry the bagasse treated in the water bath to make the natural moisture content of the bagasse < 8%;
[0053] (2) Bagasse steam explosion pulping: put the bagasse processed by blast drying in step (1) into the steam explosion pulping equipment, first inject water vapor to pressurize to 1.5MPa, keep the pressure for 8min, and then Increase the pressure to 1.7MPa, immediately open the valve to release the pressure, blast the bagasse into a cotton-like bagasse slurry, and carry out blast drying treatment on the obtained bagasse slurry again, so that the natural moisture of the bagasse slurry is <4%. Then the bagasse slurry is pulverized to 80 mesh to obtain bagasse slurry powder;
[0054] (3) Ultrasonic separation: Add the bagasse slurry powder obtained in step (2) into dist...
Embodiment 3
[0060] The method for separating lignin from bagasse, concrete operations are as follows:
[0061] (1) Bagasse pretreatment: first put the bagasse into a water bath at 90°C for 20 minutes, and then dry the bagasse treated in the water bath to make the natural moisture content of the bagasse < 8%;
[0062] (2) Bagasse steam explosion pulping: Put the bagasse processed by blast drying in step (1) into the steam explosion pulping equipment, first inject steam to pressurize to 1.3MPa, keep the pressure for 8min, and then Increase the pressure to 1.5MPa, immediately open the valve to release the pressure, blast the bagasse into a cotton-like bagasse slurry, and carry out blast drying treatment on the obtained bagasse slurry again, so that the natural moisture of the bagasse slurry is <4%. Then the bagasse slurry is pulverized to 80 mesh to obtain bagasse slurry powder;
[0063] (3) Ultrasonic separation: Add the bagasse slurry powder obtained in step (2) into distilled water and s...
PUM
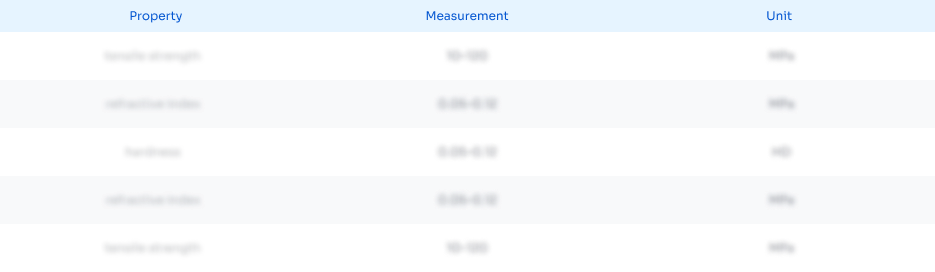
Abstract
Description
Claims
Application Information

- Generate Ideas
- Intellectual Property
- Life Sciences
- Materials
- Tech Scout
- Unparalleled Data Quality
- Higher Quality Content
- 60% Fewer Hallucinations
Browse by: Latest US Patents, China's latest patents, Technical Efficacy Thesaurus, Application Domain, Technology Topic, Popular Technical Reports.
© 2025 PatSnap. All rights reserved.Legal|Privacy policy|Modern Slavery Act Transparency Statement|Sitemap|About US| Contact US: help@patsnap.com