Organic silicon hydrolysate pyrolysis method and device of solvent oil thermal drive circulation
A technology of cracking device and solvent oil, applied in the directions of silicon organic compounds, chemical instruments and methods, chemical/physical processes, etc., to achieve the effects of good flow stability, enhanced heat transfer, and short heat transfer distance
- Summary
- Abstract
- Description
- Claims
- Application Information
AI Technical Summary
Problems solved by technology
Method used
Image
Examples
Embodiment 1
[0038] 30,000 tons / year dimethyl hydrolyzate thermal drive circulation cracking kettle
[0039] When the thermal drive circulation type cracking kettle of the present invention is used as 30,000 tons / year dimethyl hydrolyzate cracking, 1 ton of hydrolyzate needs 0.4 ton of steam, hydrolyzate: 50% KOH solution (volume)=1:0.01, product purity: D. 4 ≥99.5%, DMC (D 4 +D 5 ) ≥ 86.5%, the heat exchange area needs to be 80m after heat calculation 2 , the size of the spiral plate heat exchanger its structure see figure 1 , figure 2 .
[0040] After being preheated, the mixture of dimethyl hydrolyzate and KOH solution enters the cracking kettle from the lower feed port 106, enters the corresponding cracking channel 122 through the upper nozzle of the liquid distributor 104 and mixes with solvent oil, and absorbs heat from the heat exchange channel 121 , vaporize while reacting, the rise of the bubbles drives the liquid in the cracking channel to rise to the top of the cracking...
Embodiment 2
[0044] 55,000 tons / year dimethyl hydrolyzate heat drive circulation cracking kettle
[0045] When the thermal drive circulation type cracking kettle of the present invention is used as 55,000 tons / year dimethyl hydrolyzate cracking, 1 ton of hydrolyzate needs 0.392 tons of steam, hydrolyzate: 50% KOH solution (volume)=1:0.009, product purity: D. 4 ≥99.5%, DMC (D 4 +D 5 )≥86.7%, the heat exchange area needs to be 150m after heat calculation 2 , the size of the spiral plate heat exchanger its structure see figure 1 , figure 2 .
[0046] After being preheated, the mixture of dimethyl hydrolyzate and KOH solution enters the cracking kettle from the lower feed port 106, enters the corresponding cracking channel 122 through the upper nozzle of the liquid distributor 104 and mixes with solvent oil, and absorbs heat from the heat exchange channel 121 , vaporize while reacting, the rise of the bubbles drives the liquid in the cracking channel to rise to the top of the cracking...
PUM
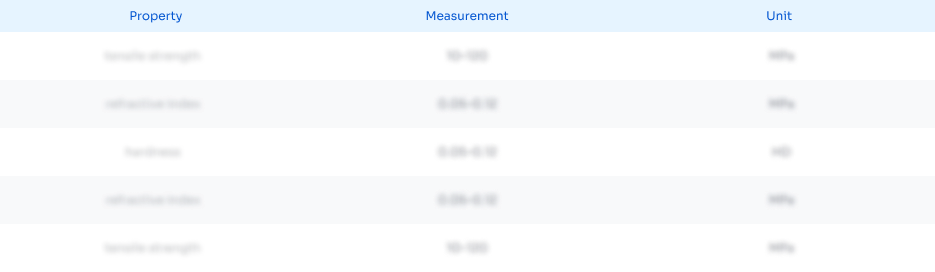
Abstract
Description
Claims
Application Information

- R&D
- Intellectual Property
- Life Sciences
- Materials
- Tech Scout
- Unparalleled Data Quality
- Higher Quality Content
- 60% Fewer Hallucinations
Browse by: Latest US Patents, China's latest patents, Technical Efficacy Thesaurus, Application Domain, Technology Topic, Popular Technical Reports.
© 2025 PatSnap. All rights reserved.Legal|Privacy policy|Modern Slavery Act Transparency Statement|Sitemap|About US| Contact US: help@patsnap.com