High-strength SMC composite material resistant to strong acid and base and grid manufacturing method using material
A composite material, strong acid and alkali technology, applied in chemical instruments and methods, applications, household components, etc., can solve the problems of low interlayer shear force, poor anisotropy, low production efficiency, etc. High tensile strength, strong acid and alkali corrosion resistance, and high mechanical compressive strength
- Summary
- Abstract
- Description
- Claims
- Application Information
AI Technical Summary
Problems solved by technology
Method used
Image
Examples
Embodiment 1
[0029] A kind of SMC composite material, it is characterized in that it comprises upper polyethylene film layer, upper resin paste layer, chopped glass fiber layer, continuous glass fiber layer, lower resin paste layer and lower polyethylene film layer arranged in sequence from top to bottom The composition of the upper resin paste layer and the lower resin paste layer is the same and consists of the following materials in parts by weight: 60 parts of novolac modified vinyl resins that can be used for magnesium oxide thickening, 40 parts of low-shrinkage additives, nano-scale 100 parts of barium sulfate powder, 4 parts of magnesium oxide paste thickener, 1 part of curing agent BPO, 4 parts of coupling agent, 3 parts of color paste, the magnesium oxide paste thickener is composed of RA-150 magnesium oxide and styrene The weight ratio is 40:60.
[0030] The low-shrinkage additive is made of WACKER POLYMER company's solid, colorless or slightly yellow name VINNAPA SC341 polymer c...
Embodiment 2
[0034] On the basis of Example 1, only change the component distribution ratio of the upper resin paste layer and the lower resin paste layer, 70 parts of vinyl resin, 30 parts of low shrinkage additives, 150 parts of nano-scale barium sulfate powder, magnesium oxide paste thickener 2.5 parts, 2 parts of curing agent BPO, 2 parts of coupling agent, 5 parts of color paste.
Embodiment 3
[0036] On the basis of Example 1, only change the component distribution ratio of the upper resin paste layer and the lower resin paste layer, 65 parts of vinyl resin, 35 parts of low shrinkage additives, 125 parts of nano-scale barium sulfate powder, magnesium oxide paste thickener 3 parts, curing agent BPO 1.5 parts, coupling agent 3 parts, color paste 4 parts. .
[0037] A method for making an SMC composite material, comprising the following steps: Step 1: by weight, 60-70 parts of vinyl resin, 30-40 parts of low-shrinkage additive, 100-150 parts of nanoscale barium sulfate powder, magnesium oxide 2.5-4 parts of paste thickener, 1.0-2.0 parts of curing agent BPO, 2-4 parts of coupling agent, 3-5 parts of color paste. , put into the mixing kettle, set the mixing kettle rotating speed 1200rpm, and stir for 20 minutes.
[0038] Step 2: Transfer the mixture obtained by stirring in step 1 to the storage tank, and transport it to the online mixer through the flow pump A, add th...
PUM
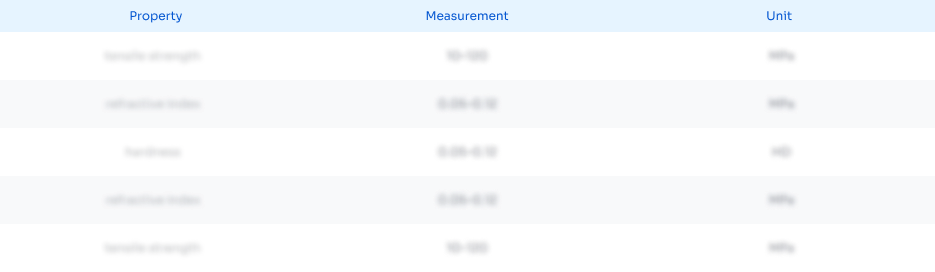
Abstract
Description
Claims
Application Information

- Generate Ideas
- Intellectual Property
- Life Sciences
- Materials
- Tech Scout
- Unparalleled Data Quality
- Higher Quality Content
- 60% Fewer Hallucinations
Browse by: Latest US Patents, China's latest patents, Technical Efficacy Thesaurus, Application Domain, Technology Topic, Popular Technical Reports.
© 2025 PatSnap. All rights reserved.Legal|Privacy policy|Modern Slavery Act Transparency Statement|Sitemap|About US| Contact US: help@patsnap.com