Machining method of irregular shell component inner cavity bottom annular groove
A processing method and technology of annular grooves, applied in the field of processing annular grooves at the bottom of the inner cavity of irregular shell components, can solve the problems of poor processing quality, poor processing rigidity, low processing efficiency, etc., and achieve stable processing state and processing stability Good, good surface quality effect
- Summary
- Abstract
- Description
- Claims
- Application Information
AI Technical Summary
Problems solved by technology
Method used
Image
Examples
Embodiment Construction
[0046] The technical solutions of the present invention will be clearly and completely described below in conjunction with the accompanying drawings.
[0047] The method for processing the annular groove at the bottom of the inner cavity of the irregular shell member according to the present invention is characterized in that it includes the following steps:
[0048] The first step is to customize the tool;
[0049] 1) According to the size and accuracy requirements of the annular groove 31 that needs to be processed at the bottom of the inner cavity 30 of the irregular shell member 3, the milling cutter 1 for rough machining the annular groove is customized, see figure 1 with figure 2The milling cutter 1 is composed of a shank 10, a cutter body 11 and a cutting edge 12; The diameter of the ring groove is smaller than the width of the ring groove, and the unilateral margin of the ring groove after milling is guaranteed to be 0.5mm (mm);
[0050] 2) According to the size an...
PUM
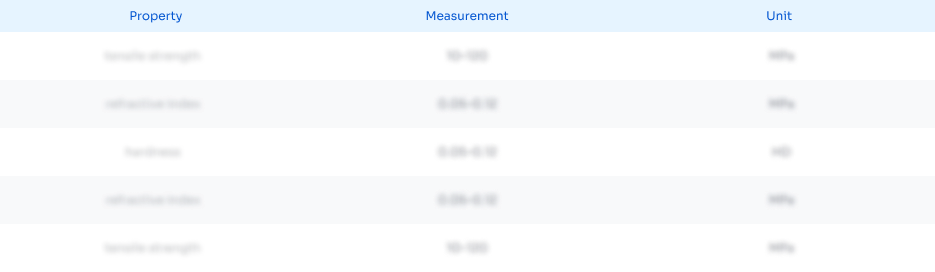
Abstract
Description
Claims
Application Information

- R&D
- Intellectual Property
- Life Sciences
- Materials
- Tech Scout
- Unparalleled Data Quality
- Higher Quality Content
- 60% Fewer Hallucinations
Browse by: Latest US Patents, China's latest patents, Technical Efficacy Thesaurus, Application Domain, Technology Topic, Popular Technical Reports.
© 2025 PatSnap. All rights reserved.Legal|Privacy policy|Modern Slavery Act Transparency Statement|Sitemap|About US| Contact US: help@patsnap.com