A new fine beneficiation process of magchitropite mixed iron ore
A technology of iron ore and new technology, which is applied in the field of fine beneficiation, the beneficiation of magchitropic mixed iron ore, and the high-efficiency field of magtropic mixed iron ore, which can solve the problem of long process route, difficult operation and large cycle and other problems, to achieve the effect of simple process flow structure, less chemical consumption, and less grinding operations
- Summary
- Abstract
- Description
- Claims
- Application Information
AI Technical Summary
Problems solved by technology
Method used
Image
Examples
Embodiment Construction
[0030] In order to further describe the present invention, a new process for fine beneficiation of maggotite mixed iron ore of the present invention will be further described in detail below in conjunction with the accompanying drawings and examples.
[0031] See Table 1 for the chemical multi-element analysis results of the magchitropite mixed iron ore, and see Table 2 for the iron phase analysis results.
[0032] Table 1 Results of chemical multi-element analysis of magchitropite mixed iron ore
[0033] Laboratory items TF S Fe FeO SiO 2
al 2 o 3
CaO content(%) 41.82 41.62 18.04 13.36 3.19 7.93 Laboratory items MgO S P K 2 o
Na 2 o
burn out content(%) 2.19 1.00 0.31 0.47 0.43 10.67
[0034] Table 2 Analysis results of iron phase of mixed iron ore
[0035] mineral name Iron phase iron content (%) Occupancy (%) magnetite 21.32 50.81 Red (brown) iron ore 16.00 38.13 ...
PUM
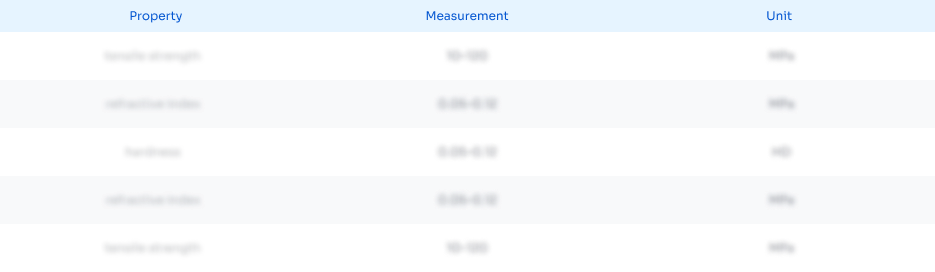
Abstract
Description
Claims
Application Information

- Generate Ideas
- Intellectual Property
- Life Sciences
- Materials
- Tech Scout
- Unparalleled Data Quality
- Higher Quality Content
- 60% Fewer Hallucinations
Browse by: Latest US Patents, China's latest patents, Technical Efficacy Thesaurus, Application Domain, Technology Topic, Popular Technical Reports.
© 2025 PatSnap. All rights reserved.Legal|Privacy policy|Modern Slavery Act Transparency Statement|Sitemap|About US| Contact US: help@patsnap.com