Low-phosphorus low-sulfur high-alloy thick plate blank smelting process
A technology for thick slabs and alloys, which is applied in the smelting process of producing low-phosphorus, low-sulfur, high-alloy thick slabs, and the smelting process of low-phosphorus, low-sulfur, high-alloy thick slabs, achieving high yield, excellent quality, and high investment. less effect
- Summary
- Abstract
- Description
- Claims
- Application Information
AI Technical Summary
Problems solved by technology
Method used
Examples
Embodiment 1
[0016] Steel type high-alloy die steel 738H, the process route adopted is: hot metal desulfurization pretreatment - converter smelting - tapping alloying - LF furnace refining and alloying - RH vacuum refining - thick slab continuous casting, the specific steps and parameters are as follows, The ingredients involved are mass percentages:
[0017] (1) Phosphorus content control: the converter is smelted by double slag method, the carbon drawing temperature is controlled at 1620°C, and the phosphorus content at the end of the converter is controlled at 0.0080%; the subsequent alloying phosphorus increase is controlled at 0.005%; the phosphorus content of the finished steel is controlled at 0.013%.
[0018] (2) Sulfur content control: [S] in hot metal after pretreatment of molten iron = 0.0050%; high-quality steel scrap and auxiliary materials are used for converter smelting, and the sulfur content of scrap steel is controlled to 0.0050%; sulfur content at the end of the converte...
Embodiment 2
[0023] Steel type high-alloy medium manganese steel, the process route adopted is: hot metal desulfurization pretreatment-converter smelting-tapping alloying-LF furnace refining and alloying-RH vacuum refining-thick slab continuous casting, the specific steps and parameters are as follows, The ingredients involved are mass percentages:
[0024] (1) Phosphorus content control: The converter is smelted by double slag method, the carbon pulling temperature is controlled at 1600°C, and the phosphorus content at the end of the converter is controlled at 0.0070%; the subsequent alloying phosphorus increase is controlled at 0.0075%; the phosphorus content of the finished steel is controlled at 0.0145%.
[0025] (2) Sulfur content control: [S] in molten iron after pretreatment of molten iron = 0.0040%; high-quality steel scrap and auxiliary materials are used for converter smelting, and the sulfur content of scrap steel is controlled to 0.0050%; sulfur content at the end of the conver...
PUM
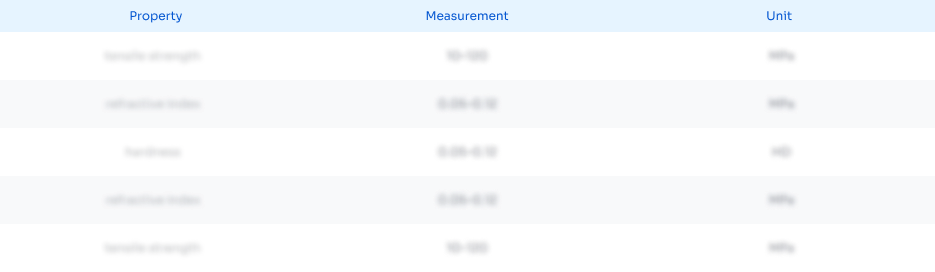
Abstract
Description
Claims
Application Information

- R&D
- Intellectual Property
- Life Sciences
- Materials
- Tech Scout
- Unparalleled Data Quality
- Higher Quality Content
- 60% Fewer Hallucinations
Browse by: Latest US Patents, China's latest patents, Technical Efficacy Thesaurus, Application Domain, Technology Topic, Popular Technical Reports.
© 2025 PatSnap. All rights reserved.Legal|Privacy policy|Modern Slavery Act Transparency Statement|Sitemap|About US| Contact US: help@patsnap.com