Ni-Cr-Al-Cu porous material and manufacturing method thereof
A technology of porous material and synthesis method, applied in the direction of electrode, electrode shape/type, electrolysis process, etc., can solve the problems of poor corrosion resistance, high electrocatalytic activity, high maintenance cost, etc., and achieve high open porosity, electrocatalytic High activity and long service life
- Summary
- Abstract
- Description
- Claims
- Application Information
AI Technical Summary
Problems solved by technology
Method used
Image
Examples
Embodiment 1
[0024] The four high-purity element powders of Ni, Cr, Al, and Cu were prepared according to the mass percentage, wherein the Cr content was 25%, the powder particle size was 5µm; the Al content was 13%, the powder particle size was 300 mesh; the Cu content was 7 %, the powder particle size is 9µm; the balance is Ni powder with a powder particle size of 6µm. Put the prepared powder on a V-type powder mixer and mix it at a constant speed for 9 hours, then add stearic acid of 1% of the total powder mass, dry for 8 hours, and cold press at a pressure of 50 MPa under a cold press for 120 seconds; Place the pressed sample in a vacuum furnace at a vacuum of 2×10 -3 In the case of Pa, maintain a heating rate of 10°C / min from room temperature to 280°C and keep it for 120 minutes; then raise the temperature to 580°C at a heating rate of 8°C / min and keep it for 180 minutes; then raise the temperature at a heating rate of 4 / min to 880°C and keep at this temperature for 60min; finally ra...
Embodiment 2
[0027] The four high-purity element powders of Ni, Cr, Fe, and Co are prepared according to mass percentage, wherein the Cr content is 20%, the powder particle size is 3µm; the Al content is 10%, the powder particle size is 300 mesh; the Cu content is 5 %, the powder particle size is 5µm; the balance is Ni powder with a powder particle size of 5µm. Put the prepared powder on a V-type powder mixer and mix it at a constant speed for 12 hours, then add stearic acid of 2% of the total mass of the powder, dry it for 10 hours, and cold press it at a pressure of 100 MPa under a cold press for 90 seconds; Place the pressed sample in a vacuum furnace at a vacuum of 1×10 -3 In the case of Pa, keep the heating rate of 15°C / min from room temperature to 300°C and keep it for 140min; then raise the temperature to 600°C at the rate of 10°C / min and keep it for 160min; then raise the temperature at the rate of 5°C / min to 950°C and keep at this temperature for 80 minutes; finally raise the tem...
Embodiment 3
[0030]The four high-purity element powders of Ni, Cr, Al, and Cu were prepared according to the mass percentage, wherein the Cr content was 20%, the powder particle size was 7µm; the Al content was 7%, the powder particle size was 300 mesh; the Cu content was 6 %, the powder particle size is 5µm; the balance is Ni powder with a powder particle size of 9µm. Put the prepared powder on a V-type powder mixer and mix it at a constant speed for 8 hours, then add stearic acid of 3% of the total powder mass, dry for 12 hours, and cold-press at a pressure of 150 MPa under a cold press for 60 seconds; Place the pressed sample in a vacuum furnace at a vacuum degree of 3×10 -3 In the case of Pa, maintain a heating rate of 11°C / min from room temperature to 270°C and keep it for 120 minutes; then raise the temperature to 580°C at a heating rate of 9°C / min and keep it for 180 minutes; then raise the temperature at a heating rate of 5°C / min to 900°C and keep at this temperature for 90 minute...
PUM
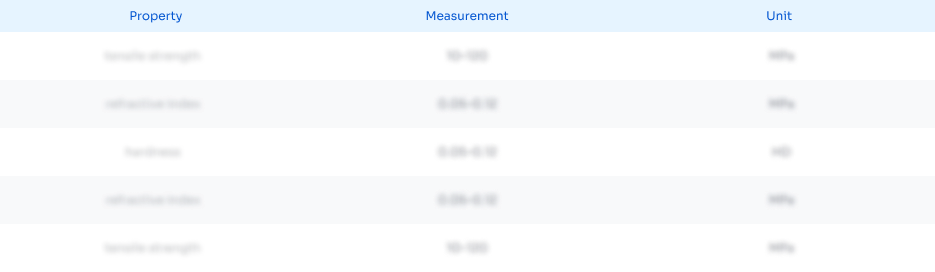
Abstract
Description
Claims
Application Information

- R&D Engineer
- R&D Manager
- IP Professional
- Industry Leading Data Capabilities
- Powerful AI technology
- Patent DNA Extraction
Browse by: Latest US Patents, China's latest patents, Technical Efficacy Thesaurus, Application Domain, Technology Topic, Popular Technical Reports.
© 2024 PatSnap. All rights reserved.Legal|Privacy policy|Modern Slavery Act Transparency Statement|Sitemap|About US| Contact US: help@patsnap.com