Melamine production device and production technology
A melamine and production device technology, applied in the field of melamine preparation, can solve problems such as increased coal consumption, high energy consumption, energy waste, etc., and achieve the effects of reducing energy consumption and waste, simple production process flow, and reasonable energy utilization
- Summary
- Abstract
- Description
- Claims
- Application Information
AI Technical Summary
Problems solved by technology
Method used
Image
Examples
Embodiment 1
[0042] like figure 2Shown, a kind of melamine production process, specifically, described production process comprises the following steps:
[0043] 1) Pump molten urea into the reactor inlet, atomize it under the action of atomizing gas and send it into the reactor. Under the gauge pressure of 0.4MPa and high temperature of 380℃, it will be catalyzed by silica gel to generate melamine, ammonia and carbon dioxide. . The heat required for the reaction is provided by the recovered reaction gas and the reactor carrier gas, that is, the molten salt heats the reactor carrier gas and the recovered reaction gas in the carrier gas heater and sends them into the reactor to provide heat for the reaction. The carrier gas of the reactor is ammonia and carbon dioxide with a volume ratio of 2:1;
[0044] 2) After the reaction is completed, the catalyst powder entrained in the reaction gas is recovered in the cyclone separator in the reactor, and then these gases are introduced into the h...
Embodiment 2
[0048] like figure 2 Shown, a kind of melamine production process, specifically, described production process comprises the following steps:
[0049] 1) Pump molten urea into the reactor inlet, atomize it under the action of atomizing gas and send it into the reactor. Under the gauge pressure of 0.6MPa and high temperature of 350℃, melamine and ammonia will be generated after being catalyzed by silica-alumina gel ,carbon dioxide. The heat required for the reaction is provided by the recovered reaction gas and the reactor carrier gas, that is, the molten salt heats the reactor carrier gas and the recovered reaction gas in the carrier gas heater and sends them into the reactor to provide heat for the reaction. The carrier gas of the reactor is ammonia and carbon dioxide with a volume ratio of 2:1;
[0050] 2) After the reaction is completed, the catalyst powder entrained in the reaction gas is recovered in the cyclone separator in the reactor, and then these gases are introdu...
Embodiment 3
[0054] like figure 2 Shown, a kind of melamine production process, specifically, described production process comprises the following steps:
[0055] 1) Pump molten urea into the reactor inlet, atomize it under the action of atomizing gas and send it into the reactor. Under the gauge pressure of 0.2MPa and high temperature of 420℃, it will be catalyzed by silica gel to generate melamine, ammonia and carbon dioxide. . The heat required for the reaction is provided by the recovered reaction gas and the reactor carrier gas, that is, the molten salt heats the reactor carrier gas and the recovered reaction gas in the carrier gas heater and sends them into the reactor to provide heat for the reaction. The carrier gas of the reactor is ammonia and carbon dioxide with a volume ratio of 2:1;
[0056] 2) After the reaction is completed, the catalyst powder entrained in the reaction gas is recovered in the cyclone separator in the reactor, and then these gases are introduced into the ...
PUM
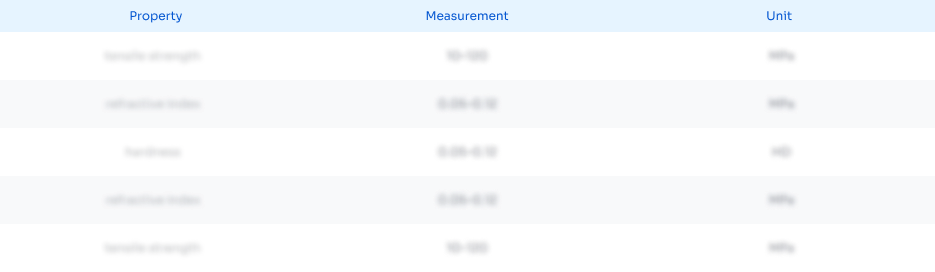
Abstract
Description
Claims
Application Information

- R&D
- Intellectual Property
- Life Sciences
- Materials
- Tech Scout
- Unparalleled Data Quality
- Higher Quality Content
- 60% Fewer Hallucinations
Browse by: Latest US Patents, China's latest patents, Technical Efficacy Thesaurus, Application Domain, Technology Topic, Popular Technical Reports.
© 2025 PatSnap. All rights reserved.Legal|Privacy policy|Modern Slavery Act Transparency Statement|Sitemap|About US| Contact US: help@patsnap.com