Composite pre-treatment technology for improving wind power gear gas carburizing efficiency
A gas carburizing and pretreatment technology, used in heat treatment furnaces, heat treatment equipment, metal material coating processes, etc., can solve problems such as technical research, achieve good hardness gradient, shorten carburizing time, and increase carburized layer thickness. Effect
- Summary
- Abstract
- Description
- Claims
- Application Information
AI Technical Summary
Problems solved by technology
Method used
Image
Examples
Embodiment 1
[0025] (1) Process 20CrMnMo steel into M8 tooth-shaped samples;
[0026] (2) The sample is subjected to quenching and tempering treatment. First, the temperature is raised to 860°C for 15 minutes, then the sample is immediately put into oil to cool, and then the temperature is raised to 670°C for 30 minutes. Cool to room temperature after taking out;
[0027] (3) Place the sample on the YS05-C20A laser shock strengthening test platform, set the laser wavelength to 1064nm, and the spot diameter to φ3mm. The surface of the sample uses 100μm black tape as the energy absorption layer, and the spot overlap rate is 50%. The pulse width is 10ns, and the laser energy is 3J to perform laser shock on the sample;
[0028] (4) Put the sample after laser shock into the multi-purpose furnace, raise the temperature of the furnace to 300°C, let in air, and pre-oxidize for 30 minutes.
[0029] (5) Heat the multi-purpose furnace to 800°C, keep it warm for 2 hours, maintain 0.4% carbon potenti...
Embodiment 2
[0033] (1) Process 20CrMnMo steel into M8 tooth-shaped samples;
[0034] (2) The sample is subjected to quenching and tempering treatment. First, the temperature is raised to 860°C for 15 minutes, then the sample is immediately put into oil to cool, and then the temperature is raised to 670°C for 30 minutes. Cool to room temperature after taking out;
[0035] (3) Place the sample on the YS05-C20A laser shock strengthening test platform, set the laser wavelength to 1064nm, and the spot diameter to φ3mm. The surface of the sample uses 100μm black tape as the energy absorption layer, and the spot overlap rate is 50%. The pulse width is 10ns, and the laser energy is 10J to perform laser shock on the sample;
[0036] (4) Put the sample after laser shock into the multipurpose furnace, raise the temperature of the furnace to 300°C, let in air, and pre-oxidize for 30 minutes.
[0037] (5) Heat the multi-purpose furnace to 800°C, keep it warm for 2 hours, maintain 0.4% carbon potenti...
Embodiment 3
[0041] (1) Process 20CrMnMo steel into M8 tooth-shaped samples;
[0042] (2) The sample is subjected to quenching and tempering treatment. First, the temperature is raised to 860°C for 15 minutes, then the sample is immediately put into oil to cool, and then the temperature is raised to 670°C for 30 minutes. Cool to room temperature after taking out;
[0043] (3) Place the sample on the YS05-C20A laser shock strengthening test platform, set the laser wavelength to 1064nm, and the spot diameter to φ3mm. The surface of the sample uses 100μm black tape as the energy absorption layer, and the spot overlap rate is 50%. The pulse width is 30ns, and the laser energy is 10J to perform laser shock on the sample;
[0044] (4) Put the sample after laser shock into the multipurpose furnace, raise the temperature of the furnace to 300°C, let in air, and pre-oxidize for 30 minutes.
[0045] (5) Heat the multi-purpose furnace to 800°C, keep it warm for 2 hours, maintain 0.4% carbon potenti...
PUM
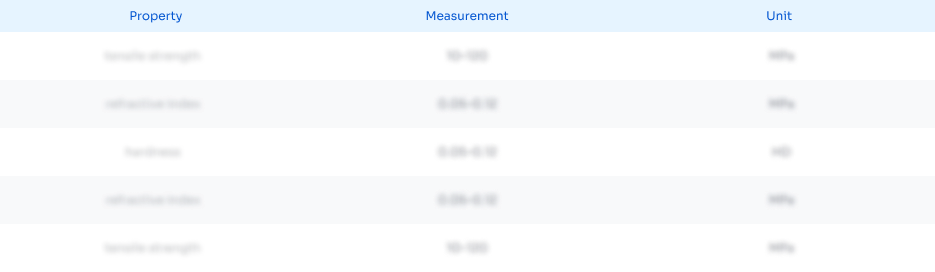
Abstract
Description
Claims
Application Information

- Generate Ideas
- Intellectual Property
- Life Sciences
- Materials
- Tech Scout
- Unparalleled Data Quality
- Higher Quality Content
- 60% Fewer Hallucinations
Browse by: Latest US Patents, China's latest patents, Technical Efficacy Thesaurus, Application Domain, Technology Topic, Popular Technical Reports.
© 2025 PatSnap. All rights reserved.Legal|Privacy policy|Modern Slavery Act Transparency Statement|Sitemap|About US| Contact US: help@patsnap.com