Electroplating pearl nickel color difference optimizing process
A pearl nickel and process technology, which is applied in the direction of metal material coating process, superimposed layer plating, coating, etc., can solve problems such as poor conductivity, product color difference, and increase product color, so as to reduce color fluctuation and improve Product qualification rate and the effect of ensuring electrical conductivity
- Summary
- Abstract
- Description
- Claims
- Application Information
AI Technical Summary
Problems solved by technology
Method used
Image
Examples
Embodiment 1
[0022] The chromatic aberration optimization process of electroplating pearl nickel on the automotive central control trim in this embodiment includes degreasing, coarsening, recycling, two-stage reduction, palladium activation, debonding, electroless nickel plating, copper pre-plating, copper plating, acid activation, and semi-plating Bright nickel, pearl nickel plating, chromium plating, reduction, ultraviolet sterilization, wind cutting and drying processes, among which the previous process is followed by water washing to the next process.
[0023] The process of plating pearl nickel is specifically: sending the semi-bright nickel-plated automotive central control trim to a special pearl nickel tank for pearl nickel plating, and the pearl nickel plating is specifically carried out under the following component solutions and conditions: sulfuric acid Nickel 460g / L, nickel chloride 43g / L, boric acid 43g / L, softener BSI 16ml / L, wetting agent MA-80 0.8ml / L, pearl nickel sand agent ...
Embodiment 2
[0026] The chromatic aberration optimization process of electroplating pearl nickel on the automotive central control trim in this embodiment includes degreasing, coarsening, recycling, two-stage reduction, palladium activation, debonding, electroless nickel plating, copper pre-plating, copper plating, acid activation, and semi-plating Bright nickel, pearl nickel plating, chromium plating, reduction, ultraviolet sterilization, wind cutting and drying processes, among which the previous process is followed by water washing to the next process.
[0027] The process of plating pearl nickel is specifically: sending the semi-bright nickel-plated automotive central control trim to a special pearl nickel tank for pearl nickel plating, and the pearl nickel plating is specifically carried out under the following component solutions and conditions: sulfuric acid Nickel 470g / L, nickel chloride 47g / L, boric acid 47g / L, softener BSI 24ml / L, wetting agent MA-80 1.6ml / L, pearl nickel sand agent ...
Embodiment 3
[0030] The chromatic aberration optimization process of electroplating pearl nickel on the automotive central control trim in this embodiment includes degreasing, coarsening, recycling, two-stage reduction, palladium activation, debonding, electroless nickel plating, copper pre-plating, copper plating, acid activation, and semi-plating Bright nickel, pearl nickel plating, chromium plating, reduction, ultraviolet sterilization, wind cutting and drying processes, among which the previous process is followed by water washing to the next process.
[0031] The process of plating pearl nickel is specifically: sending the semi-bright nickel-plated automotive central control trim to a special pearl nickel tank for pearl nickel plating, and the pearl nickel plating is specifically carried out under the following component solutions and conditions: sulfuric acid Nickel 465g / L, nickel chloride 45g / L, boric acid 45g / L, softener BSI 20ml / L, wetting agent MA-80 1.2ml / L, pearl nickel sand agent ...
PUM
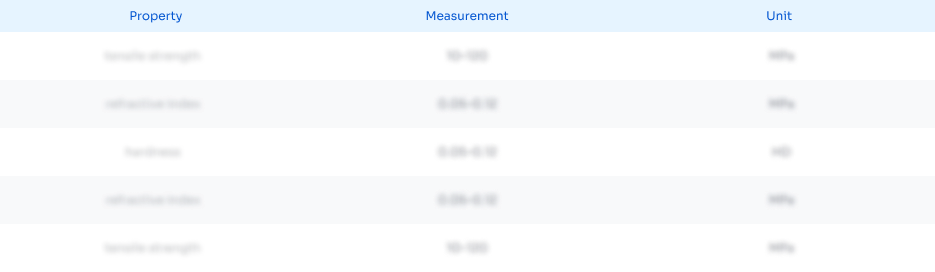
Abstract
Description
Claims
Application Information

- Generate Ideas
- Intellectual Property
- Life Sciences
- Materials
- Tech Scout
- Unparalleled Data Quality
- Higher Quality Content
- 60% Fewer Hallucinations
Browse by: Latest US Patents, China's latest patents, Technical Efficacy Thesaurus, Application Domain, Technology Topic, Popular Technical Reports.
© 2025 PatSnap. All rights reserved.Legal|Privacy policy|Modern Slavery Act Transparency Statement|Sitemap|About US| Contact US: help@patsnap.com