Brazing material for repairing anode steel claw and preparation method thereof
A technology of anode steel claws and brazing materials, applied in welding/cutting medium/material, welding equipment, welding medium, etc., can solve the problems of affecting electrolysis efficiency, high resistivity, and anode carbon block falling off, and improve the contact area. , the effect of increasing the specific surface area and reducing the anode pressure drop
- Summary
- Abstract
- Description
- Claims
- Application Information
AI Technical Summary
Problems solved by technology
Method used
Image
Examples
Embodiment 1
[0035] A brazing material for repairing anode steel claws, the brazing material includes a cylindrical brazing filler metal 3 and a semi-annular brazing filler metal 4 that are matched with the anode steel claw head 1 to be repaired and the round steel 2 for repairing , The corrosion section of the anode steel claw head 1 to be repaired is cut off, the lower end is processed with a boss 101, the round steel 2 replacing the corrosion section has the same diameter and the same length as the anode steel claw head 1, and a groove 201 is processed at the upper end. The cylindrical solder 3 is placed in the groove 201, and the semi-annular solder 4 is placed on the edge of the groove 201 of the round steel;
[0036] The cylindrical brazing filler metal 3 is formed by a thin strip of brazing filler metal 6 coated with a flux layer 5 on the surface, which is folded multiple times along the length direction into a short strip of brazing filler metal 7 with alternating brazing filler metal ...
Embodiment 2
[0052] A brazing material for repairing anode steel claws, the brazing material includes a cylindrical brazing filler metal 3 and a semi-annular brazing filler metal 4 that are matched with the anode steel claw head 1 to be repaired and the round steel 2 for repairing , The corrosion section of the anode steel claw head 1 to be repaired is removed, the lower end is processed with a boss 101, the round steel 2 replacing the corrosion section has the same diameter and the same length as the anode steel claw head 1, and a groove 201 is processed at the upper end. The cylindrical solder 3 is placed in the groove 201, and the semi-annular solder 4 is placed on the edge of the groove 201 of the round steel;
[0053] The cylindrical brazing filler metal 3 is a thin strip of brazing filler metal 6 coated with a flux layer 5 on its surface, which is folded several times along the length direction into a short strip of brazing filler metal 7 with alternating brazing filler metal and brazing...
Embodiment 3
[0069] A brazing material for repairing anode steel claws, the brazing material includes a cylindrical brazing filler metal 3 and a semi-annular brazing filler metal 4 that are matched with the anode steel claw head 1 to be repaired and the round steel 2 for repairing , The corrosion section of the anode steel claw head 1 to be repaired is removed, the lower end is processed with a boss 101, the round steel 2 replacing the corrosion section has the same diameter and the same length as the anode steel claw head 1, and a groove 201 is processed at the upper end. The cylindrical solder 3 is placed in the groove 201, and the semi-annular solder 4 is placed on the edge of the groove 201 of the round steel;
[0070] The cylindrical brazing filler metal 3 is a thin strip of brazing filler metal 6 coated with a flux layer 5 on its surface, which is folded several times along the length direction into a short strip of brazing filler metal 7 with alternating brazing filler metal and brazing...
PUM
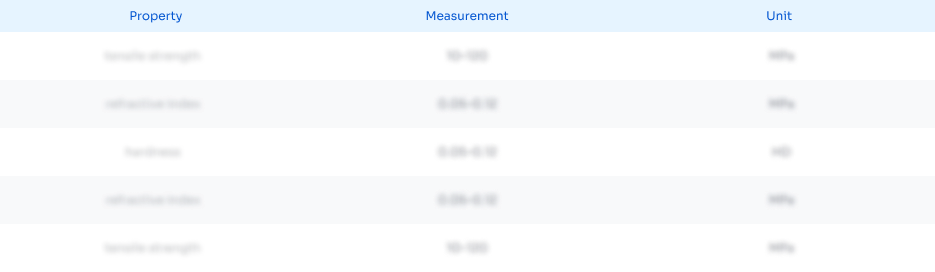
Abstract
Description
Claims
Application Information

- R&D
- Intellectual Property
- Life Sciences
- Materials
- Tech Scout
- Unparalleled Data Quality
- Higher Quality Content
- 60% Fewer Hallucinations
Browse by: Latest US Patents, China's latest patents, Technical Efficacy Thesaurus, Application Domain, Technology Topic, Popular Technical Reports.
© 2025 PatSnap. All rights reserved.Legal|Privacy policy|Modern Slavery Act Transparency Statement|Sitemap|About US| Contact US: help@patsnap.com