Molding curing agent and preparation process and application thereof
A preparation process and curing agent technology, applied in casting molding equipment, manufacturing tools, casting molds, etc., can solve the problems of high risk factor, strength, stability, insufficient high temperature resistance, and inability to improve the weather resistance of coated sand. The preparation process is simple, the curing time is shortened, and the effect of preventing agglomeration
- Summary
- Abstract
- Description
- Claims
- Application Information
AI Technical Summary
Problems solved by technology
Method used
Examples
Embodiment 1
[0031] The preparation process of molding curing agent in the present embodiment comprises the following steps:
[0032] A. Add 10 parts of phenolic resin, 8 parts of polyvinyl butyral, 4 parts of polyvinyl alcohol, 5 parts of water-soluble silicone oil, and 5 parts of paraffin oil into the mixer, and mix and stir at a temperature of 80 ° C. After mixing and stirring for 10 min, mixture A was obtained;
[0033] B. Add 3 parts of triethanolamine, 10 parts of polyacrylamide, 2 parts of coconut oil amine, 4 parts of carboxymethyl cellulose, and 6 parts of molybdenum disulfide into a stirring tank with a stirring rate of 1000 rpm for mixing and stirring. After mixing and stirring for 20 minutes, mixture B was obtained;
[0034] C. Add the above mixture B to the above mixture A, then add 4 parts of acrylic resin powder, 3 parts of titanium dioxide and 20 parts of deionized water, mix them and add them to a water bath, and heat them in a water bath at a temperature of 52°C. And ke...
Embodiment 2
[0036] The preparation process of molding curing agent in the present embodiment comprises the following steps:
[0037] A. Add 20 parts of phenolic resin, 18 parts of polyvinyl butyral, 12 parts of polyvinyl alcohol, 10 parts of water-soluble silicone oil, and 15 parts of paraffin oil into the mixer, and mix and stir at a temperature of 120 ° C. Mixture A was obtained after mixing and stirring for 20 minutes;
[0038] B, 8 parts of triethanolamine, 20 parts of polyacrylamide, 8 parts of coconut oil amine, 12 parts of carboxymethyl cellulose, and 12 parts of molybdenum disulfide are added to a stirring tank with a stirring rate of 3000 rpm for mixing and stirring, After mixing and stirring for 30 minutes, mixture B was obtained;
[0039] C. Add the above mixture B to the above mixture A, then add 10 parts of acrylic resin powder, 9 parts of titanium dioxide and 30 parts of deionized water, mix them and add them to a water bath, and heat them in a water bath at a temperature o...
Embodiment 3
[0041] The preparation process of molding curing agent in the present embodiment comprises the following steps:
[0042] A. Add 12 parts of phenolic resin, 9 parts of polyvinyl butyral, 5 parts of polyvinyl alcohol, 6 parts of water-soluble silicone oil, and 7 parts of paraffin oil into the mixer, and mix and stir at a temperature of 85 ° C. Mixture A was obtained after mixing and stirring for 12 minutes;
[0043] B. Add 4 parts of triethanolamine, 12 parts of polyacrylamide, 3 parts of coconut oil amine, 6 parts of carboxymethyl cellulose, and 7 parts of molybdenum disulfide into a stirring tank with a stirring speed of 1500 rpm for mixing and stirring. After mixing and stirring for 22 minutes, mixture B was obtained;
[0044] C. Add the above mixture B to the above mixture A, then add 5 parts of acrylic resin powder, 4 parts of titanium dioxide and 22 parts of deionized water, mix them and add them to a water bath, and heat them in a water bath at a temperature of 54°C. An...
PUM
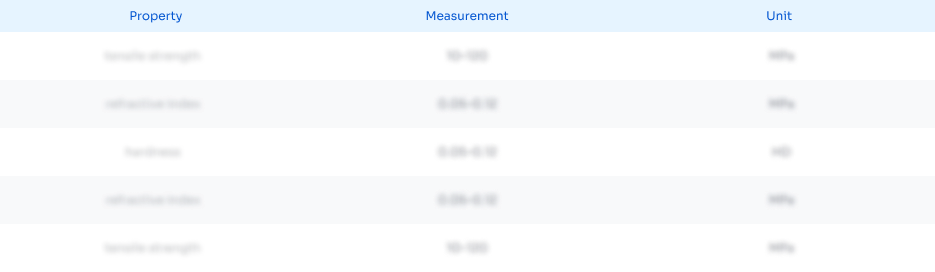
Abstract
Description
Claims
Application Information

- R&D
- Intellectual Property
- Life Sciences
- Materials
- Tech Scout
- Unparalleled Data Quality
- Higher Quality Content
- 60% Fewer Hallucinations
Browse by: Latest US Patents, China's latest patents, Technical Efficacy Thesaurus, Application Domain, Technology Topic, Popular Technical Reports.
© 2025 PatSnap. All rights reserved.Legal|Privacy policy|Modern Slavery Act Transparency Statement|Sitemap|About US| Contact US: help@patsnap.com