A kind of carbon nitride/kaolinite composite material and its preparation method and application
A composite material, kaolinite technology, applied in chemical instruments and methods, chemical/physical processes, special compound water treatment, etc. degree of effect
- Summary
- Abstract
- Description
- Claims
- Application Information
AI Technical Summary
Problems solved by technology
Method used
Image
Examples
Embodiment 1
[0041] Step 1: Measure dimethyl sulfoxide and deionized water and mix together a total of 100 mL into a beaker, the ratio of which is 10:1 (mass ratio).
[0042] Step 2. Weigh 10g of kaolinite and add it to the above mixed solvent, and stir it in a water bath at 60°C for 4 hours to obtain a viscous turbid liquid. After cooling to room temperature, wash it repeatedly with deionized water and absolute ethanol. intercalation solvent (the total washing time is 2 h), and the washed sample is dried at 60° C. for 24 h to obtain kaolinite intercalated with dimethyl sulfoxide.
[0043] Step 3: Weigh 1 g of kaolinite intercalated with dimethyl sulfoxide, grind it with 5 g of urea and 0.5 mL of deionized water for 15 min, and then keep it at 95° C. for 12 h to obtain kaolinite intercalated with urea.
[0044] Step 4: Put the kaolinite intercalated with urea into the crucible and cover it tightly with a lid, then put the crucible into the muffle furnace for roasting, cool down to room tem...
Embodiment 2
[0048] Step 1: Measure dimethyl sulfoxide and deionized water and mix together a total of 100 mL into a beaker, the ratio of which is 10:1 (mass ratio).
[0049] Step 2. Weigh 10g of kaolinite and add it to the above mixed solvent, and stir it in a water bath at 60°C for 4 hours to obtain a viscous turbid liquid. After cooling to room temperature, wash it repeatedly with deionized water and absolute ethanol. intercalation solvent (the total washing time is 1.5 h), and the washed sample was dried at 60° C. for 24 h to obtain kaolinite intercalated with dimethyl sulfoxide.
[0050] Step 3: Weighing 1 g of kaolinite intercalated with dimethyl sulfoxide, grinding it with 10 g of urea and 0.5 mL of deionized water for 15 minutes, and then keeping it at 95° C. for 12 hours to obtain kaolinite intercalated with urea.
[0051] Step 4: Put the kaolinite intercalated with urea into the crucible and cover it tightly with a lid, then put the crucible into the muffle furnace for roasting, ...
Embodiment 3
[0055] Step 1: Measure dimethyl sulfoxide and deionized water and mix together a total of 100 mL into a beaker, the ratio of which is 10:1 (mass ratio).
[0056] Step 2. Weigh 10g of kaolinite and add it to the above mixed solvent, and stir it in a water bath at 60°C for 4 hours to obtain a viscous turbid liquid. After cooling to room temperature, wash it repeatedly with deionized water and absolute ethanol. intercalation solvent (the total washing time is 2 h), and the washed sample is dried at 60° C. for 24 h to obtain kaolinite intercalated with dimethyl sulfoxide.
[0057] Step 3: Weigh 1 g of kaolinite intercalated with dimethyl sulfoxide, grind it with 15 g of urea and 0.5 mL of deionized water for 15 minutes, and then keep it at 95° C. for 12 hours to obtain kaolinite intercalated with urea.
[0058] Step 4: Put the kaolinite intercalated with urea into the crucible and cover it tightly with a lid, then put the crucible into the muffle furnace for roasting, cool down to...
PUM
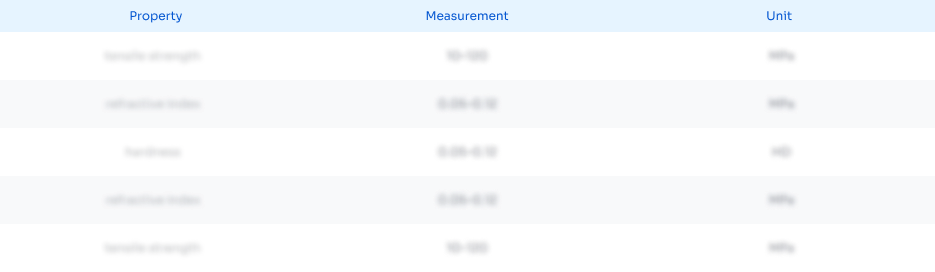
Abstract
Description
Claims
Application Information

- Generate Ideas
- Intellectual Property
- Life Sciences
- Materials
- Tech Scout
- Unparalleled Data Quality
- Higher Quality Content
- 60% Fewer Hallucinations
Browse by: Latest US Patents, China's latest patents, Technical Efficacy Thesaurus, Application Domain, Technology Topic, Popular Technical Reports.
© 2025 PatSnap. All rights reserved.Legal|Privacy policy|Modern Slavery Act Transparency Statement|Sitemap|About US| Contact US: help@patsnap.com