A kind of anti-cracking agent for surface layer and preparation method thereof
A technology of anti-cracking agent and surface layer, which is applied in the direction of coating, manufacturing tools, casting and molding equipment, etc., and can solve the problems of long drying time, increased production cost, and reduced production efficiency
- Summary
- Abstract
- Description
- Claims
- Application Information
AI Technical Summary
Problems solved by technology
Method used
Image
Examples
Embodiment 1
[0029] A surface layer anti-cracking agent, comprising the following components by weight percentage:
[0030]
[0031] The preparation method of above-mentioned surface layer anti-cracking agent comprises the following steps:
[0032] (1) Mix polyacrylamide and polyethylene glycol uniformly to obtain mixture A;
[0033] (2) Add mixture A to ethylene glycol under stirring condition, and mix uniformly to obtain mixture B;
[0034] (3) Add the mixture into pure influent water and stir for 24 hours until the mixture is uniform to obtain compound C;
[0035] (4) Add isopropanol polyoxyethylene ether into mixture C, stir until evenly mixed, and obtain compound D;
[0036] (5) Add the polyether defoamer defoamer to compound D, stir until the mixture is uniform, and then the surface layer anti-cracking agent is obtained.
Embodiment 2
[0038] A surface layer anti-cracking agent, comprising the following components by weight percentage:
[0039]
[0040]
[0041] The preparation method of above-mentioned surface layer anti-cracking agent comprises the following steps:
[0042] (1) Mix polyacrylamide and polyethylene glycol uniformly to obtain mixture A;
[0043] (2) Add mixture A to ethylene glycol under stirring condition, and mix uniformly to obtain mixture B;
[0044] (3) Add the mixture into pure influent water and stir for 26 hours until the mixture is uniform to obtain compound C;
[0045] (4) Add isopropanol polyoxyethylene ether into mixture C, stir until evenly mixed, and obtain compound D;
[0046] (5) Add the polyether defoamer defoamer to compound D, stir until the mixture is uniform, and then the surface layer anti-cracking agent is obtained.
Embodiment 3
[0048] A surface layer anti-cracking agent, comprising the following components by weight percentage:
[0049]
[0050] The preparation method of above-mentioned surface layer anti-cracking agent comprises the following steps:
[0051] (1) Mix polyacrylamide and polyethylene glycol uniformly to obtain mixture A;
[0052] (2) Add mixture A to ethylene glycol under stirring condition, and mix uniformly to obtain mixture B;
[0053] (3) Add the mixture into pure influent water, stir for 25 hours until the mixture is uniform, and obtain compound C;
[0054] (4) Add isopropanol polyoxyethylene ether into mixture C, stir until evenly mixed, and obtain compound D;
[0055] (5) Add the polyether defoamer to the compound D, stir until the mixture is uniform, and obtain the anti-cracking agent for the surface layer.
PUM
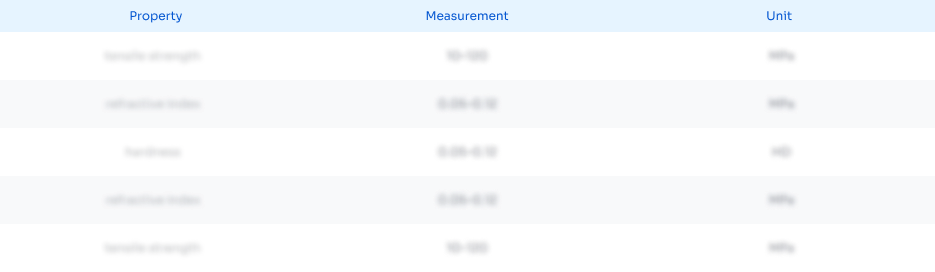
Abstract
Description
Claims
Application Information

- R&D Engineer
- R&D Manager
- IP Professional
- Industry Leading Data Capabilities
- Powerful AI technology
- Patent DNA Extraction
Browse by: Latest US Patents, China's latest patents, Technical Efficacy Thesaurus, Application Domain, Technology Topic, Popular Technical Reports.
© 2024 PatSnap. All rights reserved.Legal|Privacy policy|Modern Slavery Act Transparency Statement|Sitemap|About US| Contact US: help@patsnap.com