Novel clavulanate pipe preparation process
A preparation process and technology for carat tubes, applied in the field of carat tubes, can solve problems such as high processing costs, safety, and hidden dangers, and achieve the effects of improving external pressure resistance, improving production safety, and crystallization tightness and uniformity
- Summary
- Abstract
- Description
- Claims
- Application Information
AI Technical Summary
Problems solved by technology
Method used
Examples
Embodiment 1
[0020] A new carat tube preparation process, the specific steps are as follows:
[0021] Step 1, mixing: select qualified raw materials, raw materials include HDPE resin, LDPE resin and color masterbatch, HDPE resin, LDPE resin and color masterbatch account for 78%, 0 and 22% of the total weight by mass, and the raw materials are according to Put the proportion into the mixing unit to mix evenly and dry, the drying time is 30 minutes, and the drying temperature is 35 degrees Celsius;
[0022] Step 2, extruding: sending the dried raw materials to the extruder, the barrel temperature of the extruder is 154 degrees Celsius, and the mold temperature of the extruder is 195 degrees Celsius;
[0023] Step 3, heating: the mold roller is heated by infrared high-frequency through an infrared heating device, and the corrugated pipe is passed through the pipe material, and the molten pipe material is coated on the outside of the bellows to form a reinforcing rib;
[0024] Step 4, Winding...
Embodiment 2
[0029] A new carat tube preparation process, the specific steps are as follows:
[0030] Step 1, mixing: select qualified raw materials, raw materials include HDPE resin, LDPE resin and short fiber masterbatch, HDPE resin, LDPE resin and color masterbatch account for 80%, 3% and 17% of the total weight by mass, Put the raw materials into the mixing unit according to the proportion, mix them evenly and dry them, the drying time is 50 minutes, and the drying temperature is 38 degrees Celsius;
[0031] Step 2, extruding: sending the dried raw materials to the extruder, the barrel temperature of the extruder is 154 degrees Celsius, and the mold temperature of the extruder is 195 degrees Celsius;
[0032] Step 3, heating: the mold roller is heated by infrared high-frequency through an infrared heating device, and the corrugated pipe is passed through the pipe material, and the molten pipe material is coated on the outside of the bellows to form a reinforcing rib;
[0033] Step 4, ...
Embodiment 3
[0038] A new carat tube preparation process, the specific steps are as follows:
[0039] Step 1, mixing: select qualified raw materials, put the raw materials into the mixing unit according to the proportion, mix them evenly and dry them, the drying time is 60 minutes, and the drying temperature is 40 degrees Celsius;
[0040] Step 2, extruding: sending the dried raw materials to the extruder, the barrel temperature of the extruder is 158 degrees Celsius, and the mold temperature of the extruder is 204 degrees Celsius;
[0041] Step 3, heating: the mold roller is heated to 125 degrees Celsius with infrared high-frequency by an infrared heating device, and the corrugated pipe is passed through the pipe material, and the molten pipe material is coated on the outside of the bellows to form a reinforcing rib;
[0042] Step 4, Winding: Wind the corrugated pipe on the mold drum with flat belt and O-shaped belt at the same time, and then transport the prepared PP reinforced pipe to t...
PUM
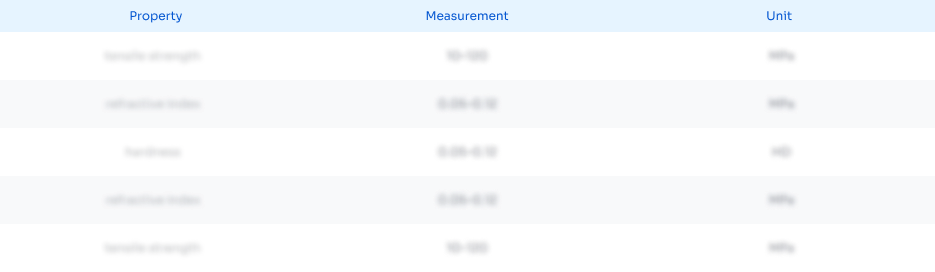
Abstract
Description
Claims
Application Information

- R&D Engineer
- R&D Manager
- IP Professional
- Industry Leading Data Capabilities
- Powerful AI technology
- Patent DNA Extraction
Browse by: Latest US Patents, China's latest patents, Technical Efficacy Thesaurus, Application Domain, Technology Topic, Popular Technical Reports.
© 2024 PatSnap. All rights reserved.Legal|Privacy policy|Modern Slavery Act Transparency Statement|Sitemap|About US| Contact US: help@patsnap.com