Modification treatment method of silicon carbide micropowder
A technology of silicon carbide micropowder and processing technology, which is applied in the direction of silicon carbide, carbide, etc., can solve the problems of insufficient modification effect and single function, achieve good compatibility and adhesion, change the dispersion state, and realize secondary modified effect
- Summary
- Abstract
- Description
- Claims
- Application Information
AI Technical Summary
Problems solved by technology
Method used
Examples
Embodiment 1
[0024] A modification treatment process of silicon carbide micropowder, comprising the steps of:
[0025] (1) Preparation of modified treatment solution:
[0026] a. Take the following materials in parts by weight: 5 parts of magnesium aluminum silicate, 4 parts of magnesium lithium silicate, 3 parts of magnesium sodium silicate, 2 parts of sodium alginate, 1 part of konjac gum, 90 parts of water;
[0027] b. Put all the raw materials weighed in operation a into the stirring tank, heat to keep the temperature in the stirring tank at 50°C, stir for 45 minutes and take out the modified treatment liquid A for later use;
[0028] c. Mix methyl behenate and glycerin into the reactor according to the molar ratio of 2.7:1, then add potassium hydroxide with a total mass of 2.2%, stir continuously for 30 minutes, and then add behenate into the reactor The total mass of methyl ester is 17% isomeric tridecyl alcohol polyoxyethylene ether, 7% polyethylene glycol, 3% sodium cetylbenzenesu...
Embodiment 2
[0040] A modification treatment process of silicon carbide micropowder, comprising the steps of:
[0041] (1) Preparation of modified treatment solution:
[0042] a. Take the following materials by weight: 7 parts of magnesium aluminum silicate, 6 parts of magnesium lithium silicate, 5 parts of magnesium sodium silicate, 4 parts of sodium alginate, 2 parts of konjac gum, 95 parts of water;
[0043] b. Put all the raw materials weighed in operation a into the stirring tank together, heat to keep the temperature in the stirring tank at 53°C, and take out the modified treatment solution A after stirring for 48 minutes;
[0044] c. Mix methyl behenate and glycerin into the reactor according to the molar ratio of 2.9:1, then add potassium hydroxide with a total mass of 2.4%, stir continuously for 33 minutes, then add behenate into the reactor 20% isomeric tridecyl alcohol polyoxyethylene ether, 9% polyethylene glycol, 4% sodium cetylbenzenesulfonate, 0.6% dimethyl carbonate, 6% fu...
Embodiment 3
[0056] A modification treatment process of silicon carbide micropowder, comprising the steps of:
[0057] (1) Preparation of modified treatment solution:
[0058] a. Take the following materials by weight: 8 parts of magnesium aluminum silicate, 7 parts of magnesium lithium silicate, 6 parts of magnesium sodium silicate, 5 parts of sodium alginate, 3 parts of konjac gum, 100 parts of water;
[0059] b. Put all the raw materials weighed in operation a into the mixing tank, heat to keep the temperature in the mixing tank at 55°C, and take out the modified treatment solution A after stirring for 50 minutes;
[0060] c. Mix methyl behenate and glycerin into the reaction kettle according to the molar ratio of 3.0:1, then add potassium hydroxide with a total mass of 2.5%, stir continuously for 35 minutes, and then add behenate into the reaction kettle 21% isomeric tridecyl alcohol polyoxyethylene ether, 10% polyethylene glycol, 5% sodium cetylbenzenesulfonate, 0.7% dimethyl carbona...
PUM
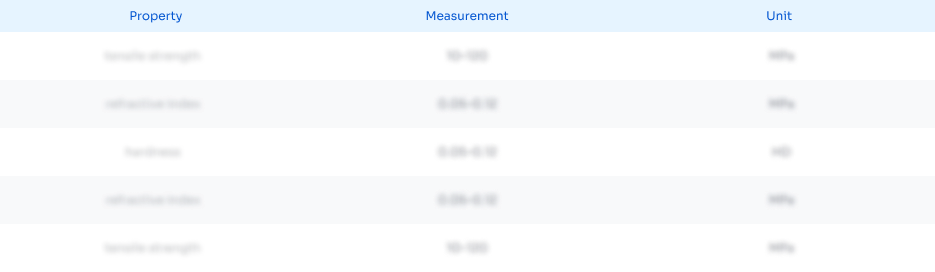
Abstract
Description
Claims
Application Information

- R&D Engineer
- R&D Manager
- IP Professional
- Industry Leading Data Capabilities
- Powerful AI technology
- Patent DNA Extraction
Browse by: Latest US Patents, China's latest patents, Technical Efficacy Thesaurus, Application Domain, Technology Topic, Popular Technical Reports.
© 2024 PatSnap. All rights reserved.Legal|Privacy policy|Modern Slavery Act Transparency Statement|Sitemap|About US| Contact US: help@patsnap.com