Cleaning type copper-aluminum composite board cold-rolled rolling oil and preparation method thereof
A copper-aluminum composite plate, cold rolling technology, applied in the petroleum industry, lubricating composition, etc., can solve the problems of less lubricating oil and expensive imported oil, improve anti-wear performance, improve surface oxidation, and ensure cleansing effect
- Summary
- Abstract
- Description
- Claims
- Application Information
AI Technical Summary
Problems solved by technology
Method used
Image
Examples
Embodiment 1
[0014] Embodiment 1 concrete each component formula is shown in the table below.
[0015]
[0016]
[0017] According to the formulation of the above components, base oil D100, lauric acid, lauryl alcohol, butyl stearate, dialkyl dithiophosphate, fatty alcohol polyethylene glycol phosphate, acidic dibutyl phosphite and dibutyl Mercaptothiadiazole is added sequentially, the weight ratio of oily agent lauric acid, lauryl alcohol and butyl stearate is 1:1:4; extreme pressure agent dialkyl dithiophosphate, fatty alcohol polyethylene glycol phosphate The weight ratio of acidic dibutyl phosphite is 3:1:1; the corrosion inhibitor dimercaptothiadiazole accounts for 0.1% of the whole oil. Put it into a reaction kettle with a rotation speed of 80-120 rpm for heating and stirring. When the temperature reaches 70-80°C, keep warm and continue stirring for 45-55 minutes, then stop heating and continue stirring to room temperature to obtain a light yellow transparent uniform oil body ...
Embodiment 2
[0019] Embodiment 1 concrete each component formula is shown in the table below.
[0020] serial number
[0021] According to the formulation of each component in Example 2, base oil D85, lauric acid, lauryl alcohol, butyl stearate, dialkyl dithiophosphate, fatty alcohol polyethylene glycol phosphate, acidic dibutyl phosphite and dimercaptothiadiazole are added sequentially, the weight ratio of oily agent lauric acid, lauryl alcohol and butyl stearate is 3:3:2; extreme pressure agent dialkyl dithiophosphate, fatty alcohol polyethylene glycol The weight ratio of phosphoric acid ester and acid dibutyl phosphite is 1:1:1; the corrosion inhibitor dimercaptothiadiazole accounts for 0.05% of the whole oil. Put it in a reaction kettle with a rotation speed of 80-120 rpm for heating and stirring. When the temperature reaches 70-80°C, keep warm and continue stirring for 45-55 minutes, then stop heating and continue stirring to room temperature to obtain a colorless, transpare...
Embodiment 3
[0023] Embodiment 1 concrete each component formula is shown in the table below.
[0024] serial number
component name
Weight (g)
1
D115
89.8
2
dialkyl dithiophosphate
0.1
3
fatty alcohol polyethylene glycol phosphate
0.3
4
Acid dibutyl phosphite
0.1
5
1.6
6
lauryl alcohol
1.6
7
6.4
8
Dimercaptothiadiazole
0.1
[0025] According to the formulations of the above components, D115, butyl stearate, lauryl alcohol, lauric acid, dialkyl dithiophosphate, fatty alcohol polyethylene glycol phosphate, acid dibutyl phosphite and dimercaptothiol Oxadiazoles are added in sequence, the weight ratio of oily agent lauric acid, lauryl alcohol and butyl stearate is 1:1:4; extreme pressure agent dialkyl dithiophosphate, fatty alcohol polyethylene glycol phosphate and acid The weight ratio of dibutyl phosphite is 1:3:1; the corrosion inhibitor dim...
PUM
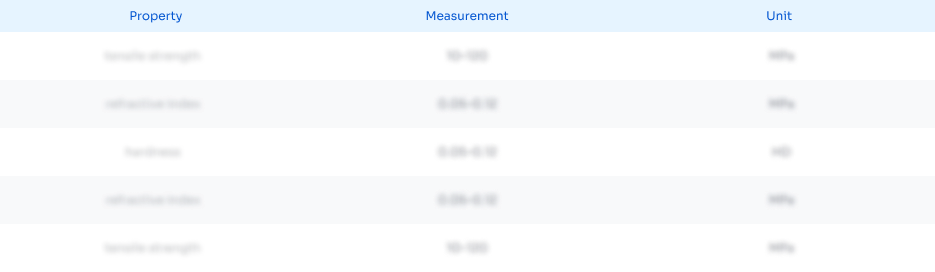
Abstract
Description
Claims
Application Information

- R&D
- Intellectual Property
- Life Sciences
- Materials
- Tech Scout
- Unparalleled Data Quality
- Higher Quality Content
- 60% Fewer Hallucinations
Browse by: Latest US Patents, China's latest patents, Technical Efficacy Thesaurus, Application Domain, Technology Topic, Popular Technical Reports.
© 2025 PatSnap. All rights reserved.Legal|Privacy policy|Modern Slavery Act Transparency Statement|Sitemap|About US| Contact US: help@patsnap.com