Manufacturing method of pipe clamp
A production method and clip technology, applied in the direction of engine components, mechanical equipment, etc., can solve the problems of easy damage, poor quality of clips, etc., achieve reliable quality, long service life, and reduce the trouble of replacement
- Summary
- Abstract
- Description
- Claims
- Application Information
AI Technical Summary
Problems solved by technology
Method used
Examples
Embodiment 1
[0014] How to make pipe clips:
[0015] 40 parts of iron-based alloy.
[0016] After decarbonization and impurity removal, a pure alloy is obtained.
[0017] Then pier the billet into a cylinder, open the flat plate to a thickness of 2 mm, then start to face it, forge it to 3 times the original density, and then start folding it in half, forging it to 6 times the original density.
[0018] During the third forging, spread a layer of 30 parts of zinc oxide, 30 parts of corundum, 3 parts of benzyl alcohol, 5 parts of alanine, 2 parts of propyl pyruvate, 6 parts of dipropylene glycol monoalkyl ether, 3- 6 parts of ethoxy ethyl propionate and 21 parts of cocamide until they are all incorporated into the material.
[0019] Then make the blank of the pipe clip, simmer at 200 degrees Celsius for 20 seconds, and then put it into an oxygen atmosphere for calcination.
[0020] Carburizing treatment is then performed on the opposite side to obtain pipe clips.
Embodiment 2
[0022] How to make pipe clips:
[0023] 80 parts of iron-based alloy.
[0024] After decarbonization and impurity removal, a pure alloy is obtained.
[0025] Then pier the billet into a cylinder, open the flat plate to a thickness of 5 mm, then start to face it, forge it to 3 times the original density, and then start folding it in half, forging it to 6 times the original density.
[0026] During the third forging, a layer of 99 parts of zinc oxide, 45 parts of corundum, 7 parts of benzyl alcohol, 17 parts of alanine, 15 parts of propyl pyruvate, 18 parts of dipropylene glycol monoalkyl ether, 3- 19 parts of ethyl ethoxy propionate and 40 parts of cocamide until they are all incorporated into the material.
[0027] Then make the blank of the pipe clip, simmer at 239 degrees Celsius for 90 seconds, and then put it into an oxygen atmosphere for calcination.
[0028] Carburizing treatment is then performed on the opposite side to obtain pipe clips.
Embodiment 3
[0030] How to make pipe clips:
[0031] 59 parts of iron-based alloy.
[0032] After decarbonization and impurity removal, a pure alloy is obtained.
[0033] Then pier the blank into a cylinder, open the flat plate to a thickness of 4mm, then start to face it, forge it to 3 times the original density, and then start folding it in half, forging it to 6 times the original density.
[0034] During the third forging, a layer of 67 parts of zinc oxide, 41 parts of corundum, 4 parts of benzyl alcohol, 12 parts of alanine, 9 parts of propyl pyruvate, 13 parts of dipropylene glycol monoalkyl ether, 3- 11 parts of ethyl ethoxy propionate and 31 parts of cocamide until they are all incorporated into the material.
[0035] Then make the blank of the pipe clip, simmer at 211 degrees Celsius for 78 seconds, and then put it into an oxygen atmosphere for calcination.
[0036] Carburizing treatment is then performed on the opposite side to obtain pipe clips.
PUM
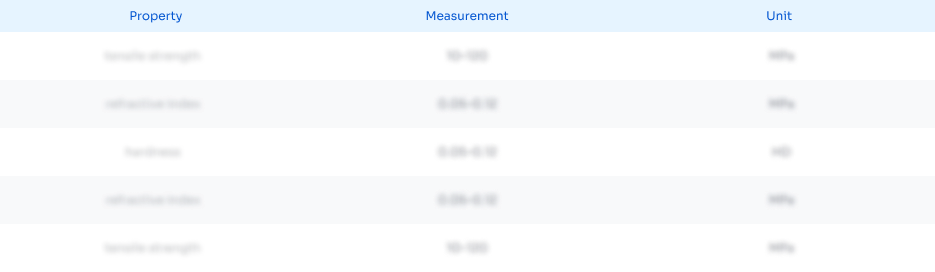
Abstract
Description
Claims
Application Information

- R&D Engineer
- R&D Manager
- IP Professional
- Industry Leading Data Capabilities
- Powerful AI technology
- Patent DNA Extraction
Browse by: Latest US Patents, China's latest patents, Technical Efficacy Thesaurus, Application Domain, Technology Topic, Popular Technical Reports.
© 2024 PatSnap. All rights reserved.Legal|Privacy policy|Modern Slavery Act Transparency Statement|Sitemap|About US| Contact US: help@patsnap.com