Calcium carbonate whisker-modified complex calcium sulphonate lubricating grease and preparation method thereof
A technology for compounding calcium sulfonate and calcium carbonate whiskers, applied in lubricating compositions, petroleum industry and other directions, can solve problems such as low price, improve mechanical stability and extreme pressure and anti-wear performance, reduce energy consumption and raw material cost , the effect of omitting the saponification and high-temperature refining steps
- Summary
- Abstract
- Description
- Claims
- Application Information
AI Technical Summary
Problems solved by technology
Method used
Image
Examples
Embodiment 1
[0039] Add 40g of 150BS (Rwe Group, the same below) and 1.5g of isopropyl dioleic acid acyloxy (dioctyl phosphate acyloxy) titanate KH-101 (Nanjing Nengde Chemical Co., Ltd. Co., Ltd.), heated and stirred to 80°C, then added 150g of calcium carbonate whisker NP-CW2 (Shanghai Fengzhu Composite New Material Technology Co., Ltd., the same below), and reacted at 85°C for 15min; then added 15g of stearic acid and continued the reaction 15min.
[0040] Add 413.5g of 150BS and 300g of high alkali value calcium sulfonate T106D into the reaction kettle with a volume of 1L, heat and stir to 85°C, then add 50g of water and 30g of glacial acetic acid in sequence, keep stirring at 95°C for 100min, the system Gradually become viscous; add the modified whisker in the above stirring container into the reaction kettle, keep at 95°C and continue to react for 10 minutes; then raise the temperature to 140°C, continue stirring for 30 minutes, and carry out dehydration reaction; after dehydration, ...
Embodiment 2
[0042] Add 45g of 120BS (Rwe Group, the same below) and 1g of isopropyl dioleic acid acyloxy (dioctyl phosphate acyloxy) titanate KH-101 into a stirring vessel with a volume of 100mL, heat and stir to 80°C , then add 70g of calcium carbonate whiskers NP-CW2, react at 85°C for 30min; then add 10g of stearic acid, and continue to react for 30min.
[0043] Add 450g of 120BS and 364g of high base value calcium sulfonate T106D into the reaction kettle with a volume of 1L, heat and stir to 90°C, then add 20g of water and 40g of glacial acetic acid in sequence, keep stirring at 100°C for 90min, the system gradually Thicken; add the modified whisker in the stirring container to the reaction kettle, keep at 100°C and continue to react for 20 minutes; then raise the temperature to 150°C, continue to stir for 25 minutes, and carry out dehydration reaction; after dehydration, the grease is cooled to 100°C and ground Homogenized degassing reaction to obtain complex calcium sulfonate grease...
PUM
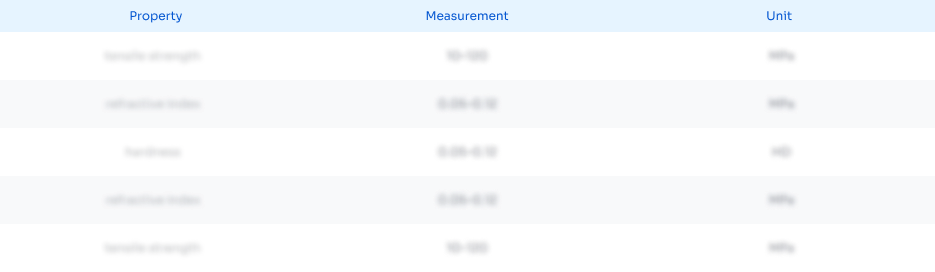
Abstract
Description
Claims
Application Information

- R&D
- Intellectual Property
- Life Sciences
- Materials
- Tech Scout
- Unparalleled Data Quality
- Higher Quality Content
- 60% Fewer Hallucinations
Browse by: Latest US Patents, China's latest patents, Technical Efficacy Thesaurus, Application Domain, Technology Topic, Popular Technical Reports.
© 2025 PatSnap. All rights reserved.Legal|Privacy policy|Modern Slavery Act Transparency Statement|Sitemap|About US| Contact US: help@patsnap.com