Zinc-rich anticorrosion coating
An anti-corrosion coating, zinc-rich technology, used in anti-corrosion coatings, conductive coatings, epoxy resin coatings, etc., can solve the problems of poor electrical conductivity and poor shielding effect of zinc powder, and achieve enhanced electrical conductivity, excellent corrosion resistance, The effect of improving adhesion and mechanical strength
- Summary
- Abstract
- Description
- Claims
- Application Information
AI Technical Summary
Problems solved by technology
Method used
Image
Examples
Embodiment 1
[0041] A zinc-rich anti-corrosion coating, the zinc-rich anti-corrosion coating is mainly composed of A component and B component with a mass ratio of 3.5:1, wherein,
[0042] The A component includes the following components in terms of mass fraction: 100 parts of inorganic nano-zinc powder, 45 parts of bisphenol S epoxy resin, 20 parts of fumed white carbon black, 10 parts of novolac epoxy resin, hydrogenated bisphenol A 15 parts of type epoxy resin, 5 parts of tetrabromobisphenol A resin, 6 parts of diglycidyl phthalate and 0.5 parts of leveling agent;
[0043] The B component includes the following components in terms of mass fraction: 50 parts of ammonia-based silicone oil, 15 parts of polyaniline, 5 parts of graphene microchips, 5 parts of boron-containing polysilane, 1 part of defoaming agent, and 0.5 parts of iodine crystal And 3 parts of wetting and dispersing agent.
Embodiment 2
[0045] A zinc-rich anti-corrosion coating, the zinc-rich anti-corrosion coating is mainly composed of A component and B component with a mass ratio of 6:1, wherein,
[0046] The A component includes the following components in terms of mass fraction: 100 parts of inorganic nano-zinc powder, 75 parts of bisphenol S epoxy resin, 35 parts of fumed white carbon black, 25 parts of novolac epoxy resin, hydrogenated bisphenol A 20 parts of type epoxy resin, 10 parts of tetrabromobisphenol A resin, 15 parts of diglycidyl phthalate and 1.5 parts of leveling agent;
[0047] The B component includes the following components in terms of mass fractions: 65 parts of ammonia-based silicone oil, 25 parts of polyaniline, 10 parts of graphene microchips, 8 parts of boron-containing polysilane, 3 parts of defoaming agent, and 0.5 parts of iodine crystal And 5 parts of wetting and dispersing agent.
Embodiment 3
[0049] A zinc-rich anti-corrosion coating, the zinc-rich anti-corrosion coating is mainly composed of A component and B component with a mass ratio of 4:1, wherein,
[0050] The A component includes the following components in terms of mass fraction: 100 parts of inorganic nano-zinc powder, 55 parts of bisphenol S epoxy resin, 25 parts of fumed white carbon black, 10 parts of novolac epoxy resin, hydrogenated bisphenol A 18 parts of type epoxy resin, 5 parts of tetrabromobisphenol A resin, 6 parts of diglycidyl phthalate and 0.5 parts of leveling agent;
[0051] The B component includes the following components in terms of mass fractions: 55 parts of ammonia-based silicone oil, 18 parts of polyaniline, 8 parts of graphene microchips, 5 parts of boron-containing polysilane, 2 parts of defoaming agent, and 0.5 parts of iodine crystal And 3 parts of wetting and dispersing agent.
PUM
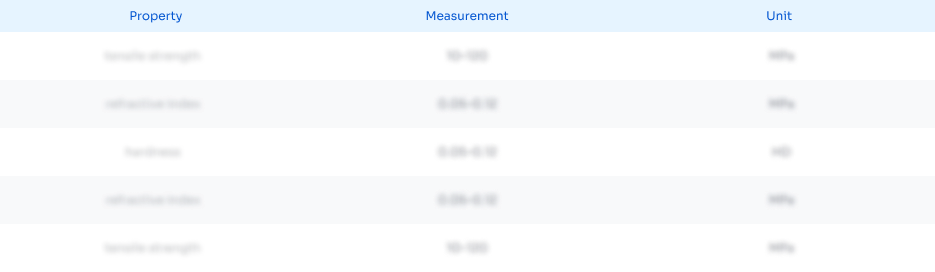
Abstract
Description
Claims
Application Information

- R&D
- Intellectual Property
- Life Sciences
- Materials
- Tech Scout
- Unparalleled Data Quality
- Higher Quality Content
- 60% Fewer Hallucinations
Browse by: Latest US Patents, China's latest patents, Technical Efficacy Thesaurus, Application Domain, Technology Topic, Popular Technical Reports.
© 2025 PatSnap. All rights reserved.Legal|Privacy policy|Modern Slavery Act Transparency Statement|Sitemap|About US| Contact US: help@patsnap.com