Method and system for collaborative smelting and recycling valuable metal from waste circuit board, scrap copper and copper-containing waste residue
A technology of waste circuit boards and valuable metals, which is applied to the improvement of process efficiency, photography technology, instruments, etc., can solve the problems of large waste liquid discharge, low product quality, and large acid and alkali consumption, and achieve recovery rate High, large quantity, no secondary pollution effect
- Summary
- Abstract
- Description
- Claims
- Application Information
AI Technical Summary
Problems solved by technology
Method used
Image
Examples
Embodiment approach
[0048] The invention adopts the combination of fire method and wet method to smelt waste circuit boards, waste miscellaneous copper and copper-containing waste slag, and comprehensively recycles and utilizes the valuable metals therein. In order to make full use of valuable metals in waste circuit boards, waste miscellaneous copper and copper-containing waste slag, such as figure 1 As shown, in the embodiment of the present invention, the three components are crushed and mixed at first, which can be crushed separately and then mixed, or mixed and then crushed. According to a preferred embodiment of the present invention, the mass ratio of the waste circuit board, waste miscellaneous copper and copper-containing waste slag is 1:3:6˜1:4:5. In the present invention, the mass ratio of waste circuit boards, waste miscellaneous copper and copper-containing waste slag is preferably controlled within the above-mentioned range, mainly because factors such as source and quantity of raw ...
Embodiment 1
[0074] Through the following steps, valuable metals such as copper, nickel, tin, iron, zinc, etc. are recovered comprehensively through collaborative smelting from waste circuit boards, waste miscellaneous copper, and copper-containing waste slag. The main components of waste circuit boards are: CuO 15%, NiO 2 %, SnO 2 4%, Fe 2 o 3 0.6%, ZnO 1%; the main components of scrap copper are: CuO 90%, NiO 0.05%, SnO 2 0.01%, Fe 2 o 3 0.25%, ZnO8%; the main components of copper-containing waste residue are: CuO 20%, NiO 1%, SnO 2 0.5%, Fe 2 o 3 15%, ZnO 0.2%.
[0075] 1) Take 100g of waste circuit boards, 300g of waste miscellaneous copper and 600g of copper-containing waste slag, crush and mix them evenly, with a mass ratio of 1:3:6, and place them in a high-temperature melting furnace at a melting temperature of 1100°C for 2 hours to obtain 507.73g of metal alloy grading 79.77% copper, 456.04g of slag and 36.23g of soot flue gas. After the flue gas is absorbed by the...
Embodiment 2
[0084] The selected waste circuit boards, miscellaneous copper waste and copper-containing waste slag are the same as in Example 1, and the main components are the same as above.
[0085] 1) Take 100g of waste circuit boards, 350g of waste miscellaneous copper and 550g of copper-containing waste slag, crush and mix them evenly, with a mass ratio of 1:3.5:5.5, and place them in a high-temperature melting furnace at a melting temperature of 1200°C for 1 hour to obtain 548.53g of metal alloy grading 80.21% copper, 408.32g of slag and 43.15g of soot flue gas. After the flue gas is absorbed by the NaOH solution with a mass concentration of 5%, the exhaust gas is obtained, which is colorless and odorless.
[0086] 2) Get 500g metal alloy to make anode sheet, then get 100g 99.99% pure copper to make cathode sheet, take the mixed solution of sulfuric acid and copper sulfate as electrolyte, copper concentration in electrolyte is 45g / L, sulfuric acid concentration is 180g / L L, the curr...
PUM
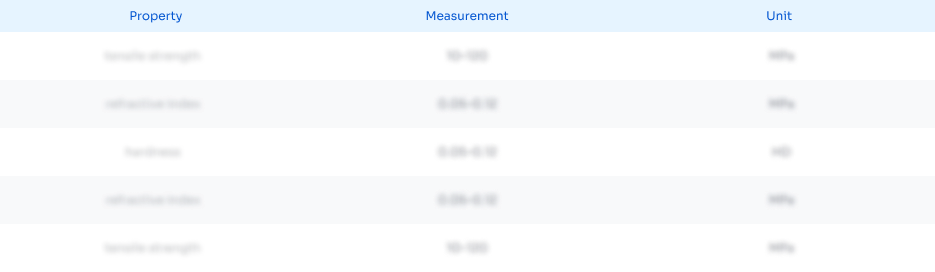
Abstract
Description
Claims
Application Information

- R&D Engineer
- R&D Manager
- IP Professional
- Industry Leading Data Capabilities
- Powerful AI technology
- Patent DNA Extraction
Browse by: Latest US Patents, China's latest patents, Technical Efficacy Thesaurus, Application Domain, Technology Topic, Popular Technical Reports.
© 2024 PatSnap. All rights reserved.Legal|Privacy policy|Modern Slavery Act Transparency Statement|Sitemap|About US| Contact US: help@patsnap.com