Method for extracting fault features of gantry crane lifting mechanism under variable speed
A portal crane and hoisting mechanism technology, which is applied in machine gear/transmission mechanism testing, machine/structural component testing, mechanical component testing, etc. It can solve problems such as inaccurate instantaneous speed curve estimation
- Summary
- Abstract
- Description
- Claims
- Application Information
AI Technical Summary
Problems solved by technology
Method used
Image
Examples
Embodiment Construction
[0025] Below, the substantive features and advantages of the present invention will be further described in conjunction with examples, but the present invention is not limited to the listed examples.
[0026] see figure 1 As shown, a method for extracting fault features of the hoisting mechanism of a portal crane under variable speed, including the following steps:
[0027] 1) In the present invention, first, the piezoelectric vibration acceleration sensor is used to pick up the original vibration signal of the hoisting mechanism of the portal crane under the variable speed.
[0028] The piezoelectric vibration acceleration sensor is installed on the bearing seat of the hoisting mechanism of the gantry crane, and after extracting the original vibration signal of the hoisting mechanism of the gantry crane, the signal is amplified and filtered by the data acquisition instrument for modulus Conversion, thereby obtaining the digital signal, can be stored in the computer according...
PUM
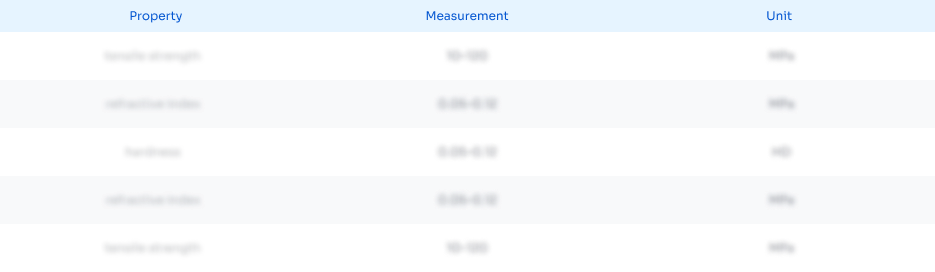
Abstract
Description
Claims
Application Information

- Generate Ideas
- Intellectual Property
- Life Sciences
- Materials
- Tech Scout
- Unparalleled Data Quality
- Higher Quality Content
- 60% Fewer Hallucinations
Browse by: Latest US Patents, China's latest patents, Technical Efficacy Thesaurus, Application Domain, Technology Topic, Popular Technical Reports.
© 2025 PatSnap. All rights reserved.Legal|Privacy policy|Modern Slavery Act Transparency Statement|Sitemap|About US| Contact US: help@patsnap.com