Smelting method capable of increasing scrap ratio of steel per ton
A smelting method and scrap steel ratio technology, which is applied in the field of iron and steel smelting to increase the steel scrap ratio per ton of steel, can solve the problems of high pressure for removing inclusions, large amount of deoxidized products, and poor ability to remove S (sulfur). The effect of improving the economic benefits of enterprises, improving product quality, and improving the purity of molten steel
- Summary
- Abstract
- Description
- Claims
- Application Information
AI Technical Summary
Problems solved by technology
Method used
Image
Examples
Embodiment 1
[0043] The operation steps of this embodiment are as follows:
[0044] a. Blast furnace ironmaking process, the temperature in the molten iron ditch of the blast furnace is 1440°C, the amount of steel scrap added in the iron gutter is 15kg / t iron, and the composition of the molten iron: Si content is 0.25%, S content is 0.047%, and P content is 0.145%;
[0045] b. Iron mixing furnace process, the temperature of the molten iron in the iron mixing furnace is 1320°C, 20kg / t iron scrap is added to the impact area of the molten iron flow during the tapping process, and the Si content of the molten iron composition is 0.30%, the S content is 0.048%, and the P content is 0.144%. ;
[0046] c. Converter steelmaking process, the amount of molten iron loaded into the converter is 61.50t, the amount of scrap steel loaded is 368kg / t iron, the amount of steel tapping is 82t, the pressure of the oxygen lance is controlled at 1.1Mpa during the smelting process, the position of the lance is...
Embodiment 2
[0052] The operation steps of this embodiment are as follows:
[0053] a. Blast furnace ironmaking process, the temperature in the molten iron trough of the blast furnace is 1480°C, the amount of steel scrap added in the molten iron trough is 18kg / t iron, and the composition of molten iron: Si content is 0.30%, S content is 0.045%, and P content is 0.149%;
[0054] b. Iron mixing furnace process, the temperature of the molten iron in the iron mixing furnace is 1330°C, and 23kg / t of scrap steel is added to the impact area of the molten iron flow during the tapping process. The Si content of the molten iron composition is 0.30%, the S content is 0.043%, and the P content is 0.147%. ;
[0055] c. Converter steelmaking process, the amount of molten iron loaded into the converter is 61.30t, the amount of scrap steel loaded is 358kg / t iron, and the amount of steel tapped is 81.75t. The pressure of the oxygen lance during the smelting process is controlled at 1.1Mpa, and the positi...
Embodiment 3
[0061] The operation steps of this embodiment are as follows:
[0062] a. Blast furnace ironmaking process, the temperature in the molten iron trough of the blast furnace is 1510°C, the amount of steel scrap added in the molten iron trough is 20kg / t of iron, and the composition of molten iron: Si content is 0.37%, S content is 0.048%, and P content is 0.150%;
[0063] b. Process of iron mixing furnace. The temperature of molten iron in the iron mixing furnace is 1350°C. During the tapping process, 25kg / t of scrap steel is added to the impact area of the molten iron flow. The content of Si in the molten iron is 0.39%, the content of S is 0.048%, and the content of P is 0.148%. ;
[0064] c. Converter steelmaking process, the amount of molten iron loaded into the converter is 61.10t, the amount of scrap steel loaded is 349kg / t iron, and the amount of steel tapped is 81.5t. The pressure of the oxygen lance during the smelting process is controlled at 1.1Mpa, and the position of...
PUM
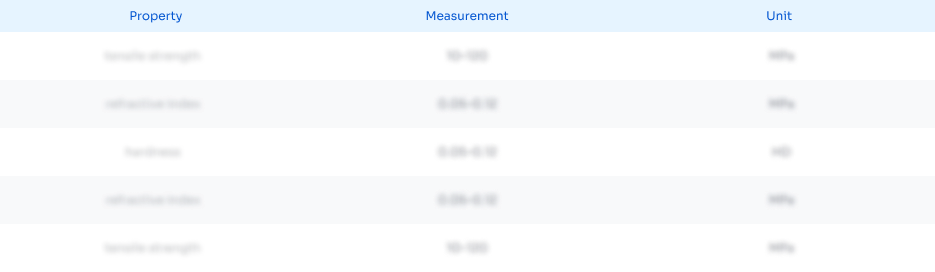
Abstract
Description
Claims
Application Information

- Generate Ideas
- Intellectual Property
- Life Sciences
- Materials
- Tech Scout
- Unparalleled Data Quality
- Higher Quality Content
- 60% Fewer Hallucinations
Browse by: Latest US Patents, China's latest patents, Technical Efficacy Thesaurus, Application Domain, Technology Topic, Popular Technical Reports.
© 2025 PatSnap. All rights reserved.Legal|Privacy policy|Modern Slavery Act Transparency Statement|Sitemap|About US| Contact US: help@patsnap.com