Medium-temperature matte glaze and preparation method thereof
A matte glaze and medium temperature technology, applied in the field of ceramic glazes, can solve the problems of strict product quality assurance, unsuitable for large-scale production, complex process requirements, etc., and achieve good ornamental, smooth touch, and strong artistry. Effect
- Summary
- Abstract
- Description
- Claims
- Application Information
AI Technical Summary
Problems solved by technology
Method used
Image
Examples
Embodiment 1
[0053] Get 20 parts in parts by weight of potassium feldspar powder, 5 parts in quartz powder, 22 parts in calcite powder, 25 parts in calcined talcum powder, 7 parts in calcined zinc oxide, 5 parts in calcined bone charcoal powder, 10 parts in calcined alumina, 2 parts in high territory, Add 4 parts of cobalt black to the ball mill for ball milling, and then add water to the ball mill. The mass ratio of raw materials: balls: water is 1:2:0.6. Among the high alumina balls, the large balls, medium balls, and small balls are divided into 2: The mass ratio of 5:3 is added to the ball mill, and the ball milling time is 24 hours. The fineness of the glaze obtained after ball milling is controlled at 0.1-0.2% of the 325 mesh sieve. After the glaze leaves the ball mill, pass through a 120-mesh sieve to obtain a glaze slurry, then measure the concentration of the glaze slurry, determine the required concentration of the glaze slurry according to different types of vessels, add water to...
Embodiment 2
[0055] Get 25 parts in parts by weight of potassium feldspar powder, 10 parts in quartz powder, 18 parts in calcite powder, 20 parts in calcined talcum powder, 5 parts in calcined zinc oxide, 5 parts in calcined bone charcoal powder, 10 parts in calcined alumina, 5 parts in high territory, Add 2 parts of red brown to the ball mill for ball milling, and then add water to the ball mill. The mass ratio of raw materials: balls: water is 1:2:0.6. Among the high alumina balls, the large balls, medium balls, and small balls are divided into 2: The mass ratio of 5:3 is added to the ball mill, and the ball milling time is 24 hours. The fineness of the glaze obtained after ball milling is controlled at 0.1-0.2% of the 325 mesh sieve. After the glaze leaves the ball mill, pass through a 120-mesh sieve to obtain the glaze slurry, then measure the concentration of the glaze slurry, determine the required concentration of the glaze slurry according to different types of vessels, add water to...
Embodiment 3
[0057] Get 30 parts in parts by weight of potassium feldspar powder, 7 parts in quartz powder, 18 parts in calcite powder, 25 parts in calcined talcum powder, 7 parts in calcined zinc oxide, 3 parts in calcined bone charcoal powder, 7 parts in calcined alumina, 2 parts in high territory, Add 1 part of malachite green to the ball mill for ball milling, and then add water to the ball mill. The mass ratio of raw materials: balls: water is 1:2:0.6. Among the high alumina balls, the large balls, medium balls, and small balls are divided into 2: The mass ratio of 5:3 is added to the ball mill, and the ball milling time is 24 hours. The fineness of the glaze obtained after ball milling is controlled at 0.1-0.2% of the 325 mesh sieve. After the glaze comes out of the ball mill, pass through a 120-mesh sieve to obtain the glaze slurry, then measure the concentration of the glaze slurry, determine the required concentration of the glaze slurry according to different types of utensils, ad...
PUM
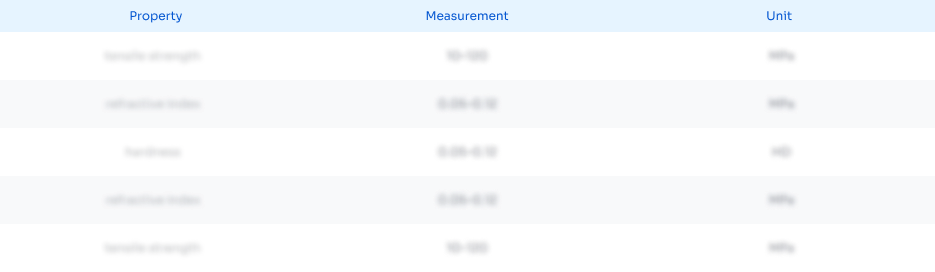
Abstract
Description
Claims
Application Information

- R&D
- Intellectual Property
- Life Sciences
- Materials
- Tech Scout
- Unparalleled Data Quality
- Higher Quality Content
- 60% Fewer Hallucinations
Browse by: Latest US Patents, China's latest patents, Technical Efficacy Thesaurus, Application Domain, Technology Topic, Popular Technical Reports.
© 2025 PatSnap. All rights reserved.Legal|Privacy policy|Modern Slavery Act Transparency Statement|Sitemap|About US| Contact US: help@patsnap.com