Production method of high-strength zeolite water-permeable bricks
A permeable brick and high-strength technology, which is applied in the field of preparation of high-strength zeolite permeable bricks, can solve the problems of poor continuous water permeability, poor filtering effect, low mechanical strength, etc., and achieve broad application prospects, enhanced cohesion, and improved mechanical strength.
- Summary
- Abstract
- Description
- Claims
- Application Information
AI Technical Summary
Problems solved by technology
Method used
Image
Examples
example 1
[0026]Select a macroporous resin with a pore diameter of 800nm and put it into a carbonization furnace, and feed nitrogen gas into the carbonization furnace at a rate of 10mL / min, heat it up to 400°C under the protection of nitrogen gas, and keep it carbonized for 2 hours to obtain a carbonized skeleton. After mixing with absolute ethanol at a mass ratio of 1:5, the shaker was shaken and impregnated for 6 hours. After the oscillation was completed, the filter residue was obtained by filtration and separation. After crushing, it was passed through a 50-mesh sieve to obtain modified carbonized skeleton particles; the mass ratio was 1:2: 10:40:120 Mix sodium metaaluminate, sodium hydroxide, modified carbonized skeleton particles, potassium thiocyanate solution with a mass fraction of 10% and deionized water, put them into a beaker to obtain a mixed solution, and move the beaker into a water bath , heat up to 70°C, continue to add 30% tetraethyl orthosilicate dropwise into the be...
example 2
[0028] Select a macroporous resin with a pore diameter of 8500nm and put it into a carbonization furnace, and feed nitrogen gas into the carbonization furnace at a rate of 10mL / min, heat it up to 450°C under the protection of nitrogen gas, and keep it carbonized for 2.5h to obtain a carbonized skeleton. Skeleton and absolute ethanol are mixed at a mass ratio of 1:5, shaken and soaked in a shaking table for 7 hours, filtered and separated to obtain a filter residue after shaking, crushed and passed through a 50-mesh sieve, and the modified carbonized skeleton particles are obtained; the mass ratio is 1:2 :10:40:120 Mix sodium metaaluminate, sodium hydroxide, modified carbonized skeleton particles, potassium thiocyanate solution with a mass fraction of 10% and deionized water, put them into a beaker to obtain a mixed solution, and put the beaker into a water bath In the pot, heat up to 75°C, continue to add 30% tetraethyl orthosilicate to the beaker dropwise, keep stirring and re...
example 3
[0030] Select a macroporous resin with a pore diameter of 900nm and put it into a carbonization furnace, and inject nitrogen gas into the carbonization furnace at a rate of 10mL / min, heat up to 500°C under the protection of nitrogen gas, and keep warm for 3 hours to obtain a carbonized skeleton. After mixing with absolute ethanol at a mass ratio of 1:5, shake the shaker and impregnate for 8 hours. After the oscillation is completed, filter and separate to obtain a filter residue. After crushing, pass through a 50-mesh sieve to obtain modified carbonized skeleton particles; the mass ratio is 1:2: 10:40:120 Mix sodium metaaluminate, sodium hydroxide, modified carbonized skeleton particles, potassium thiocyanate solution with a mass fraction of 10% and deionized water, put them into a beaker to obtain a mixed solution, and move the beaker into a water bath , heat up to 80°C, continue to add 30% tetraethyl orthosilicate dropwise into the beaker, and keep stirring for 3 hours to obt...
PUM
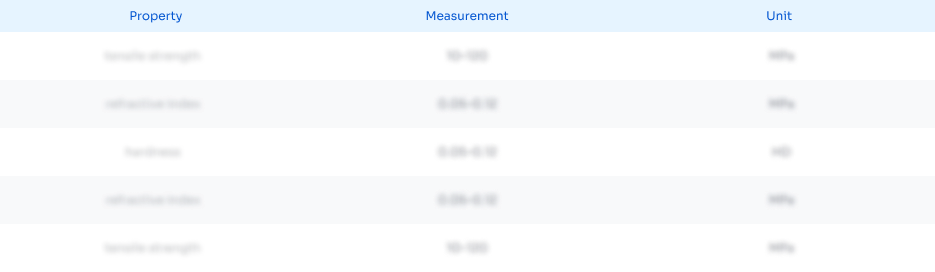
Abstract
Description
Claims
Application Information

- R&D
- Intellectual Property
- Life Sciences
- Materials
- Tech Scout
- Unparalleled Data Quality
- Higher Quality Content
- 60% Fewer Hallucinations
Browse by: Latest US Patents, China's latest patents, Technical Efficacy Thesaurus, Application Domain, Technology Topic, Popular Technical Reports.
© 2025 PatSnap. All rights reserved.Legal|Privacy policy|Modern Slavery Act Transparency Statement|Sitemap|About US| Contact US: help@patsnap.com