Separation method for rare earth elements in monazite
A rare earth element and separation method technology, which is applied in the direction of improving process efficiency, can solve problems such as difficult removal, and achieve the effect of increasing the recovery rate of rare earth
- Summary
- Abstract
- Description
- Claims
- Application Information
AI Technical Summary
Problems solved by technology
Method used
Examples
Embodiment 1
[0020] The invention provides a method for separating rare earth elements in monazite, comprising the following steps:
[0021] Step 1): firstly grind the monazite ore and mixed rare earth ore into ore powder, the particle size of the ore powder is -80um, first adopt open-circuit grinding in batches, and then use imitation closed-circuit grinding, the method is to grind the selected raw ore to After a certain period of time, sieve out products with a particle size of -70um or more, and regrind the products on the sieve. The amount of water for regrinding should be added according to the weight of the products on the sieve and the grinding concentration when grinding the raw ore. When it is above 80%, wash the ore powder with water.
[0022] Step 2): According to the ratio of monazia slag (㎏):acid (L)=1:1~15, add monazia slag to the sulfuric acid solution with a concentration of 0.25mol / L~0.5mol / L, and heat to 40 ℃ ~ 100 ℃, stirring for 5 hours to 8 hours, cooling and standing...
Embodiment 2
[0028] The invention provides a method for separating rare earth elements in monazite, comprising the following steps:
[0029] Step 1): firstly grind the monazite ore and mixed rare earth ore into ore powder, the particle size of the ore powder is -80um, first adopt open-circuit grinding in batches, and then use imitation closed-circuit grinding, the method is to grind the selected raw ore to After a certain period of time, sieve out products with a particle size of -70um or more, and regrind the products on the sieve. The amount of water for regrinding should be added according to the weight of the products on the sieve and the grinding concentration when grinding the raw ore. When it is above 80%, wash the ore powder with water.
[0030] Step 2): According to the ratio of monazia slag (㎏):acid (L)=1:1~15, add monazia slag to the sulfuric acid solution with a concentration of 0.25mol / L~0.5mol / L, and heat to 40 ℃ ~ 100 ℃, stirring for 5 hours to 8 hours, cooling and standing...
PUM
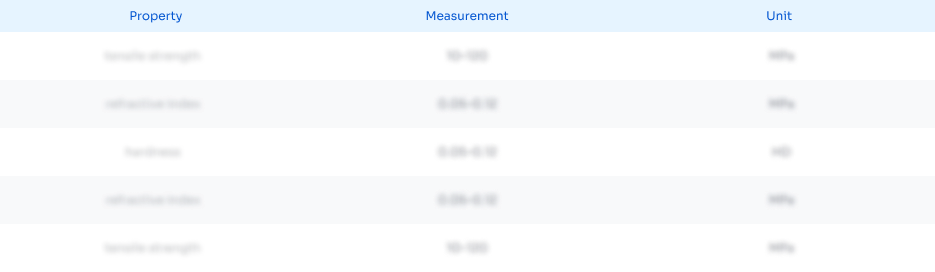
Abstract
Description
Claims
Application Information

- R&D Engineer
- R&D Manager
- IP Professional
- Industry Leading Data Capabilities
- Powerful AI technology
- Patent DNA Extraction
Browse by: Latest US Patents, China's latest patents, Technical Efficacy Thesaurus, Application Domain, Technology Topic, Popular Technical Reports.
© 2024 PatSnap. All rights reserved.Legal|Privacy policy|Modern Slavery Act Transparency Statement|Sitemap|About US| Contact US: help@patsnap.com