Anti-yellowing and ultraviolet-proof coating
An anti-ultraviolet coating and anti-yellowing technology, which is applied in coatings, anti-fouling/underwater coatings, reflection/signal coatings, etc., can solve the problems of coating yellowing and achieve the effect of improving anti-yellowing ability
- Summary
- Abstract
- Description
- Claims
- Application Information
AI Technical Summary
Problems solved by technology
Method used
Image
Examples
Embodiment 1
[0023] A preparation method for an anti-yellowing and anti-ultraviolet coating, comprising the following steps:
[0024] S1. Grinding the zinc oxide powder to the nanometer level through an ultra-fine grinder;
[0025] S2, adding the zinc oxide powder into the glass ionomer cement, stirring and mixing it with an ultrasonic mixer;
[0026] S3. Mix light stabilizer Tinuvin B 75, antioxidant IRGASTAB PUR 68, ethylene glycol, glacial acetic acid, and control the temperature at 5-10°C;
[0027] S4. Mix the product of step S2 and the product of step S3, and rapidly raise the temperature to 80° C. through infrared heating;
[0028] S5. Cool down the temperature of the product in step S4 to normal temperature, and spray it onto the lens through a nozzle to form a 200nm coating.
[0029] The content of each of the above components is
[0030] 30 parts of glass ionomer cement; 15 parts of ethylene glycol; 5 parts of glacial acetic acid; 1 part of antioxidant IRGASTAB PUR68; 1 part of...
Embodiment 2
[0032] A preparation method for an anti-yellowing and anti-ultraviolet coating, comprising the following steps:
[0033] S1. Grinding the zinc oxide powder to the nanometer level through an ultra-fine grinder;
[0034] S2, adding the zinc oxide powder into the glass ionomer cement, stirring and mixing it with an ultrasonic mixer;
[0035] S3. Mix light stabilizer Tinuvin B 75, antioxidant IRGASTAB PUR 68, ethylene glycol, glacial acetic acid, and control the temperature at 5-10°C;
[0036] S4. Mix the product of step S2 and the product of step S3, and rapidly raise the temperature to 90° C. through infrared heating;
[0037] S5. Cool down the temperature of the product in step S4 to normal temperature, and spray it onto the lens through a nozzle to form a 300nm coating.
[0038] The content of each of the above components is
[0039] 32 parts of glass ionomer cement; 18 parts of ethylene glycol; 8 parts of glacial acetic acid; 1 part of antioxidant IRGASTAB PUR68; 1 part of...
Embodiment 3
[0041] A preparation method for an anti-yellowing and anti-ultraviolet coating, comprising the following steps:
[0042] S1. Grinding the zinc oxide powder to the nanometer level through an ultra-fine grinder;
[0043] S2, adding the zinc oxide powder into the glass ionomer cement, stirring and mixing it with an ultrasonic mixer;
[0044] S3. Mix light stabilizer Tinuvin B 75, antioxidant IRGASTAB PUR 68, ethylene glycol, glacial acetic acid, and control the temperature at 5-10°C;
[0045] S4. Mix the product of step S2 and the product of step S3, and rapidly raise the temperature to 80° C. through infrared heating;
[0046] S5. Cool down the temperature of the product in step S4 to normal temperature, and spray it onto the lens through a nozzle to form a 200nm coating.
[0047] The content of each of the above components is
[0048] 35 parts of glass ionomer cement; 20 parts of ethylene glycol; 10 parts of glacial acetic acid; 3 parts of antioxidant IRGASTAB PUR68; 3 parts...
PUM
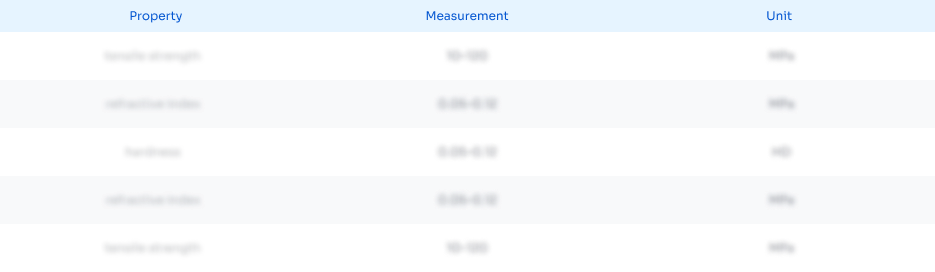
Abstract
Description
Claims
Application Information

- R&D
- Intellectual Property
- Life Sciences
- Materials
- Tech Scout
- Unparalleled Data Quality
- Higher Quality Content
- 60% Fewer Hallucinations
Browse by: Latest US Patents, China's latest patents, Technical Efficacy Thesaurus, Application Domain, Technology Topic, Popular Technical Reports.
© 2025 PatSnap. All rights reserved.Legal|Privacy policy|Modern Slavery Act Transparency Statement|Sitemap|About US| Contact US: help@patsnap.com