Machining method for special-shaped part
A technology for machining and parts, applied in the field of machining special-shaped parts, can solve the problems of difficult alignment, low processing efficiency, and high processing difficulty, and achieve the effect of reducing the requirements of production equipment and personnel skills, and low processing costs.
- Summary
- Abstract
- Description
- Claims
- Application Information
AI Technical Summary
Problems solved by technology
Method used
Examples
Embodiment 1
[0024] A method for machining special-shaped parts, comprising the following steps:
[0025] The first step is to position the special-shaped parts to be processed through the fixture to keep them accurately positioned;
[0026] The second step is to rough the fixed parts, firstly carry out rough boring of the inner hole, and then perform semi-finishing of the outer circle;
[0027] In the third step, after the turning process is completed, use an abrasive belt to grind the surface of the workpiece after turning;
[0028] The fourth step is polishing and repairing the center holes at both ends of the rough boring and polishing the whole part;
[0029] In the fifth step, the polished workpiece is placed in a chemical solution, and a layer of anti-corrosion film is coated on the surface of the workpiece through chemical action.
[0030] In use, diamond boring machines are used in each process to process the special-shaped parts, and the special-shaped end face contour and cham...
Embodiment 2
[0032] Based on Embodiment 1, a machining method for special-shaped parts comprises the following steps:
[0033] The first step is to position the special-shaped parts to be processed through the fixture to keep them accurately positioned;
[0034] The second step is to carry out rough machining on the fixed parts, first carry out rough boring of the inner hole, and then carry out semi-finishing of the outer circle, on the boring machine, with the center line as the standard, make two planes and two center holes, and then clamp on the lathe noodle;
[0035] In the third step, after the turning process is completed, use an abrasive belt to grind the surface of the workpiece after turning;
[0036] The fourth step is polishing and repairing the center holes at both ends of the rough boring and polishing the whole part;
[0037] In the fifth step, the polished workpiece is placed in a chemical solution, and a layer of anti-corrosion film is coated on the surface of the workpie...
Embodiment 3
[0039] Based on Embodiment 2, a machining method for special-shaped parts comprises the following steps:
[0040] The first step is to position the special-shaped parts to be processed through the fixture to keep them accurately positioned;
[0041] The second step is to carry out rough machining on the fixed parts, first carry out rough boring of the inner hole, and then carry out semi-finishing of the outer circle, on the boring machine, with the center line as the standard, make two planes and two center holes, and then clamp on the lathe On the surface, on the boring machine, straighten the broaching knives in the 4 holes with a diameter of 33mm to a diameter of 32mm, and punch the center holes at both ends with a margin of 0.7mm;
[0042] In the third step, after the turning process is completed, use an abrasive belt to grind the surface of the workpiece after turning;
[0043] The fourth step is polishing and repairing the center holes at both ends of the rough boring a...
PUM
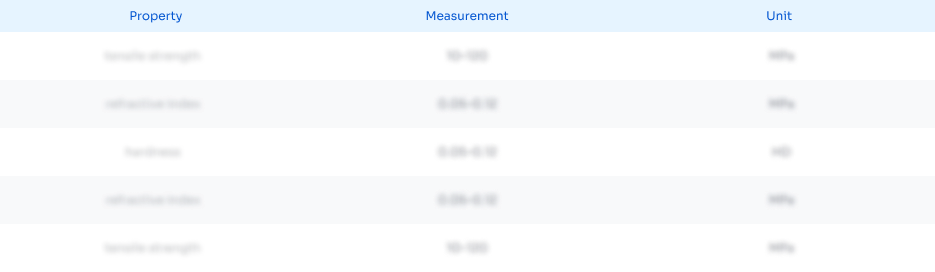
Abstract
Description
Claims
Application Information

- Generate Ideas
- Intellectual Property
- Life Sciences
- Materials
- Tech Scout
- Unparalleled Data Quality
- Higher Quality Content
- 60% Fewer Hallucinations
Browse by: Latest US Patents, China's latest patents, Technical Efficacy Thesaurus, Application Domain, Technology Topic, Popular Technical Reports.
© 2025 PatSnap. All rights reserved.Legal|Privacy policy|Modern Slavery Act Transparency Statement|Sitemap|About US| Contact US: help@patsnap.com