Non-orthogonal correction method for workpiece stage and correction device
A calibration method and technology of a calibration device, applied in the field of lithography, can solve the problems of inability to meet the requirements of the whole machine, long calibration time, far less than the frequency of mirror changes, etc.
- Summary
- Abstract
- Description
- Claims
- Application Information
AI Technical Summary
Problems solved by technology
Method used
Image
Examples
Embodiment Construction
[0034] The present invention is described in detail below in conjunction with accompanying drawing:
[0035] Such as Figure 2-4 As shown, the present invention provides a non-orthogonal correction method for a workpiece table, comprising the following steps:
[0036] S1: Set non-orthogonal measurement marks 6 on the coarse motion rotary table 7 used to carry the substrate 3 on the workpiece table 2. The non-orthogonal measurement marks 6 are provided with at least three, and are not on a straight line, so as to measure the workpiece table. 2 for on-line measurement, in this embodiment, three reflectors 4 are set on the coarse motion rotating table 7, and the three non-orthogonal measurement marks 6 are set on the three said non-orthogonal measurement marks 6 one by one On the reflecting mirror 4, there are three visual units 5 correspondingly.
[0037] S2: select three non-orthogonal measurement marks 6, move the workpiece table 2, and align the vision unit 5 with the three...
PUM
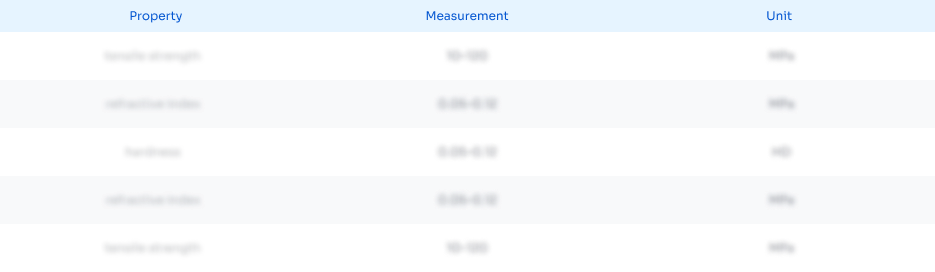
Abstract
Description
Claims
Application Information

- Generate Ideas
- Intellectual Property
- Life Sciences
- Materials
- Tech Scout
- Unparalleled Data Quality
- Higher Quality Content
- 60% Fewer Hallucinations
Browse by: Latest US Patents, China's latest patents, Technical Efficacy Thesaurus, Application Domain, Technology Topic, Popular Technical Reports.
© 2025 PatSnap. All rights reserved.Legal|Privacy policy|Modern Slavery Act Transparency Statement|Sitemap|About US| Contact US: help@patsnap.com