Modularized flue gas desulfurization, dust-removing and denitration integrated treatment system
A desulfurization and dust removal and treatment system technology, applied in the direction of gas treatment, chemical/physical process, heterogeneous catalyst chemical elements, etc., can solve the problems of high flue gas flow rate, increased energy consumption, deactivation of denitrification catalyst, etc., to achieve Effects of improving catalyst efficiency, alleviating sulfur poisoning, and improving filtration accuracy
- Summary
- Abstract
- Description
- Claims
- Application Information
AI Technical Summary
Problems solved by technology
Method used
Image
Examples
Embodiment 1
[0035] Catalyst 1 is used as a catalyst unit and assembled into an integrated catalyst module in a matrix arrangement. The three-dimensional schematic diagram of the integrated catalyst module is shown in Image 6As shown, the integrated catalyst module is respectively installed in the reaction chamber 6 of the dust removal and denitrification system in the modular flue gas desulfurization, dust removal and denitrification integrated treatment system, and then the flue gas generated in the boiler 1 is passed into the desulfurization through a closed pipe. In the tower 2, the flue gas is in contact with the calcium oxide sprayed by the nozzle 3 during the flow process, and a large amount of sulfur dioxide reacts with the calcium oxide to realize the removal of sulfur dioxide in the flue gas, and the removal efficiency is above 75%.
[0036] The flue gas after desulfurization treatment enters the reaction chamber 6 through the connecting flue and the ammonia gas sprayed from the ...
Embodiment 2
[0038] Catalyst 2 was used as a catalyst unit and assembled into an integrated catalyst module in a matrix arrangement. Referring to the method in Example 1, the final dust removal efficiency of the treatment system was 99.8%, and the denitrification efficiency was 80.2%.
Embodiment 3
[0040] Catalyst 3 was used as a catalyst unit and assembled into an integrated catalyst module in a matrix arrangement. Referring to the method in Example 1, the final dust removal efficiency of the treatment system was 99.5%, and the denitrification efficiency was 90.6%.
PUM
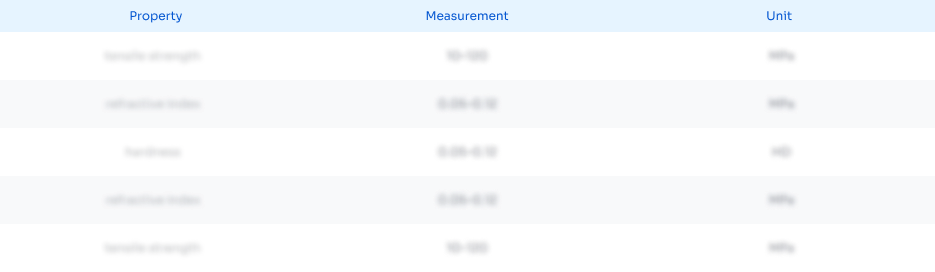
Abstract
Description
Claims
Application Information

- R&D Engineer
- R&D Manager
- IP Professional
- Industry Leading Data Capabilities
- Powerful AI technology
- Patent DNA Extraction
Browse by: Latest US Patents, China's latest patents, Technical Efficacy Thesaurus, Application Domain, Technology Topic, Popular Technical Reports.
© 2024 PatSnap. All rights reserved.Legal|Privacy policy|Modern Slavery Act Transparency Statement|Sitemap|About US| Contact US: help@patsnap.com