Oxygen functional group-enriched carbon adsorbing material and preparation method and application thereof
A technology rich in oxygen functions and oxygen functional groups, applied in chemical instruments and methods, other chemical processes, gas treatment and other directions, can solve the problems of low temperature mercury removal efficiency, etc., and achieve cheap raw materials, simple and controllable processes, and easy raw materials. the effect
- Summary
- Abstract
- Description
- Claims
- Application Information
AI Technical Summary
Problems solved by technology
Method used
Image
Examples
Embodiment 1
[0029] Grind semi-coke particles into 280-mesh coal powder; mix 120 g of coal powder with 30 g of starch and 20 g of deionized water at a stirring speed of 500 r / min, and then use a flat-die rolling granulator at 20 MPa Extruded into a cylindrical shape under pressure to obtain shaped carbon;
[0030] The above formed carbon was carbonized in a high-temperature tube furnace from room temperature to 700 °C for 2 h, then the temperature was raised to 830 °C, 20 mL / min of water vapor was introduced to activate for 1 h, and the temperature was naturally cooled to room temperature to obtain a carbon material;
[0031] Slowly drop 50 mL of concentrated nitric acid into 120 mL of deionized water, and cool the resulting solution to room temperature for later use;
[0032] Add 30 g of the above-mentioned carbon material and 70 mL of the above-mentioned acid solution into a three-necked flask. Then the remaining acid solution (100 mL) was dropped into the three-necked flask through the...
Embodiment 2
[0035] The semi-coke particles are ground into 250 mesh coal powder; 140 g of fine powder is mixed with 45 g of epoxy resin and 30 g of deionized water at a stirring speed of 400 r / min, and then rolled and granulated with a flat die at 30 Extruded into a cylindrical shape under MPa pressure to obtain shaped carbon;
[0036] The above formed carbon was carbonized in a high-temperature tube furnace from room temperature to 600 °C for 3 h, then the temperature was raised to 890 °C, 15 mL / min of water vapor was introduced to activate for 1.5 h, and the temperature was naturally cooled to room temperature to obtain a carbon material;
[0037] Slowly drop 75 mL of concentrated sulfuric acid into 90 mL of deionized water, and cool the resulting solution to room temperature for later use;
[0038] Add 45 g of the above-mentioned carbon material and 110 mL of the above-mentioned acid solution into a three-necked flask. Then, the remaining mixed acid solution (55 mL) was added into the...
Embodiment 3
[0041] The semi-coke particles are ground into coal powder of 230 mesh; 160 g of fine powder, 60 g of resole phenolic resin, and 40 g of deionized water are mixed evenly at a stirring speed of 600 r / min, and then a flat die rolling granulator is used at 40 Extruded into a cylindrical shape under MPa pressure to obtain shaped carbon;
[0042] The above formed carbon was carbonized in a high-temperature tube furnace from room temperature to 500 °C for 4 h, then the temperature was raised to 950 °C, activated by 10 mL / min water vapor for 3 h, and naturally cooled to room temperature to obtain a carbon material;
[0043] Slowly drop 100 mL of concentrated nitric acid into 60 mL of deionized water, and cool the resulting solution to room temperature for later use;
[0044]Add 60 g of the above-mentioned carbon material and 120 mL of the above-mentioned acid solution into a three-necked flask. Then the remaining acid solution (40mL) was added into the three-neck flask through the c...
PUM
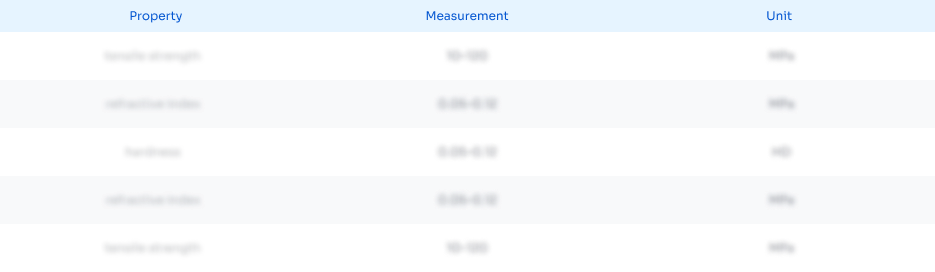
Abstract
Description
Claims
Application Information

- R&D Engineer
- R&D Manager
- IP Professional
- Industry Leading Data Capabilities
- Powerful AI technology
- Patent DNA Extraction
Browse by: Latest US Patents, China's latest patents, Technical Efficacy Thesaurus, Application Domain, Technology Topic, Popular Technical Reports.
© 2024 PatSnap. All rights reserved.Legal|Privacy policy|Modern Slavery Act Transparency Statement|Sitemap|About US| Contact US: help@patsnap.com