Preparation method of thermal insulation fiber
A thermal fiber and antistatic agent technology, which is applied in the field of textile fiber manufacturing, can solve the problems of polyester fiber thermal insulation modification is of great significance and polyester fiber thermal insulation performance is poor, and achieve good thermal insulation performance, excellent wrinkle resistance, and improved thermal insulation performance. Effect
- Summary
- Abstract
- Description
- Claims
- Application Information
AI Technical Summary
Problems solved by technology
Method used
Examples
Embodiment 1
[0027] A preparation method of thermal fiber, comprising the following steps:
[0028] a) Prepare raw materials according to the following parts by weight: 120 parts of polyethylene terephthalate, 5 parts of antistatic agent, 4 parts of smoothing agent, 20 parts of polyvinyl alcohol, 80 parts of organic solvent; the antistatic agent is fatty acid glyceride , the smoothing agent is fatty acid polyoxyethylene alcohol, the organic solvent is N,N-dimethylformamide, and the molecular weight of polyvinyl alcohol is 20000;
[0029] b) Mix and dissolve polyethylene terephthalate and an organic solvent, and vigorously stir to dissolve at 100°C for 600 minutes to prepare spinning dope A;
[0030] c) Add antistatic agent, smoothing agent and polyvinyl alcohol to spinning stock solution A, and vigorously stir at 80°C for 10 minutes to prepare spinning stock solution;
[0031] d) Transport the spinning stock solution to the spinning machine, extrude it through the spinneret and shape it i...
Embodiment 2
[0034] A preparation method of thermal fiber, comprising the following steps:
[0035] a) Prepare raw materials according to the following parts by weight: 120 parts of polyethylene terephthalate, 5.2 parts of antistatic agent, 4.5 parts of smoothing agent, 23 parts of polyvinyl alcohol, 95 parts of organic solvent; the antistatic agent is fatty acid glyceride , the smoothing agent is fatty acid polyoxyethylene alcohol, the organic solvent is N,N-dimethylformamide, and the molecular weight of polyvinyl alcohol is 23000;
[0036] b) Mix and dissolve polyethylene terephthalate and an organic solvent, and vigorously stir to dissolve at 105°C for 630 minutes to prepare spinning dope A;
[0037] c) Add antistatic agent, smoothing agent and polyvinyl alcohol to spinning stock solution A, and vigorously stir at 85°C for 12 minutes to prepare spinning stock solution;
[0038] d) Transport the spinning stock solution to the spinning machine, extrude it through the spinneret and shape ...
Embodiment 3
[0041] A preparation method of thermal fiber, comprising the following steps:
[0042] a) Prepare raw materials according to the following parts by weight: 120 parts of polyethylene terephthalate, 5.5 parts of antistatic agent, 5 parts of smoothing agent, 25 parts of polyvinyl alcohol, 110 parts of organic solvent; the antistatic agent is fatty acid glyceride , the smoothing agent is fatty acid polyoxyethylene alcohol, the organic solvent is N,N-dimethylformamide, and the molecular weight of polyvinyl alcohol is 25000;
[0043] b) Mix and dissolve polyethylene terephthalate and an organic solvent, and vigorously stir to dissolve at 110°C for 650 minutes to prepare spinning dope A;
[0044] c) Add antistatic agent, smoothing agent and polyvinyl alcohol to spinning stock solution A, and vigorously stir at 90°C for 15 minutes to prepare spinning stock solution;
[0045] d) Transport the spinning stock solution to the spinning machine, extrude it through the spinneret and shape i...
PUM
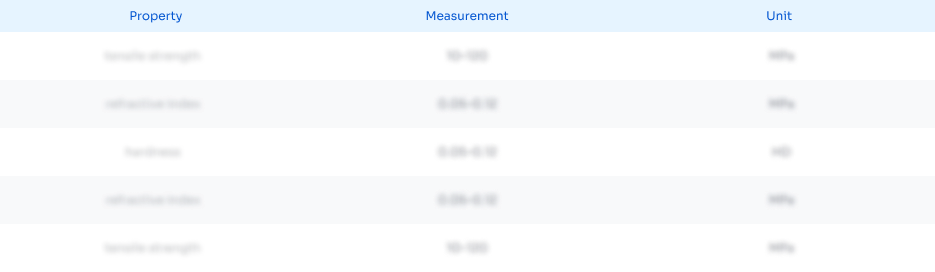
Abstract
Description
Claims
Application Information

- R&D
- Intellectual Property
- Life Sciences
- Materials
- Tech Scout
- Unparalleled Data Quality
- Higher Quality Content
- 60% Fewer Hallucinations
Browse by: Latest US Patents, China's latest patents, Technical Efficacy Thesaurus, Application Domain, Technology Topic, Popular Technical Reports.
© 2025 PatSnap. All rights reserved.Legal|Privacy policy|Modern Slavery Act Transparency Statement|Sitemap|About US| Contact US: help@patsnap.com