Method for preparing 2-alkylanthraquinone with microchannel continuous reactor
A technology of microchannel reactor and alkylanthraquinone, which is applied in chemical instruments and methods, chemical/physical/physicochemical reactors, quinone preparation, etc., can solve the problem of 2-(4-alkylbenzoyl)benzoic acid Micro-mixing is not achieved, the basic parameters of jet mixing are not given, and the processing process is complicated, etc., to achieve the effect of improving the working environment, reducing equipment investment, and simple process operation
- Summary
- Abstract
- Description
- Claims
- Application Information
AI Technical Summary
Problems solved by technology
Method used
Image
Examples
Embodiment 1
[0028] 2-(4-ethylbenzoyl)benzoic acid at 140° C. was continuously added to the T-type mixer I at a flow rate of 6.0 g / min and concentrated sulfuric acid at room temperature at a flow rate of 15 ml / min to mix, and the liquid 2- The mass (g) of (4-ethyl benzoyl) benzoic acid and concentrated sulfuric acid: the volume (ml) ratio is 1: 2.5, and the control mixing temperature is 50 ℃, and the mixture flows into the microchannel reactor I in the plug flow mode Inside, the reactor temperature is controlled at 120°C, and the residence time is 30min; the reaction liquid flowing out from the reactor directly enters the mixer II for mixing, and directly enters the microchannel reactor II for hydrolysis, and the reaction temperature is controlled at 40°C, and the residence time is 5min; then enter the separation unit for separation, the separation unit uses an equal amount of toluene for extraction, the oil phase is washed with alkali, washed with water, and distilled to obtain 2-ethylanth...
Embodiment 2
[0030]Add 2-(4-butylbenzoyl)benzoic acid at 180°C at a flow rate of 5.0g / min and room temperature concentrated sulfuric acid at a flow rate of 11ml / min to the Y-type mixer I and mix continuously, and the liquid 2- The mass (g) of (4-butyl benzoyl) benzoic acid and concentrated sulfuric acid: the volume (ml) ratio is 1: 2.2, control mixing temperature 40 ℃, the mixture flows into the microchannel reactor I with plug-flow mode Inside, the reactor temperature is controlled at 130°C, and the residence time is 20min; the reaction liquid flowing out from the reactor directly enters the mixer II for mixing, and directly enters the microchannel reactor II for hydrolysis, and the reaction temperature is controlled at 30°C, and the residence time is 10 min; then enter the separation unit for separation, the separation unit uses an equal amount of toluene for extraction, the oil phase is washed with alkali, washed with water, and distilled to obtain 2-butylanthraquinone with a yield of 80...
Embodiment 3
[0032] Add 2-(4-propylbenzoyl)benzoic acid at 140°C at a flow rate of 4.0g / min and concentrated sulfuric acid at 60°C at a flow rate of 7.6ml / min into the T-type mixer I for mixing with a metering pump. The mass (g) of 2-(4-ethyl benzoyl) benzoic acid and concentrated sulfuric acid: the volume (ml) ratio is 1:1.9, the mixing temperature is controlled at 50°C, and the mixture flows into the microchannel reaction in a plug-flow manner In the reactor I, the temperature of the reactor is controlled at 110°C, and the residence time is 30 minutes; the reaction liquid flowing out from the reactor directly enters the mixer II for mixing, and directly enters the microchannel reactor II for hydrolysis, and the reaction temperature is controlled at room temperature, and the residence time is Then enter the separation unit for separation, the separation unit uses an equal amount of toluene for extraction, the oil phase is washed with alkali, washed with water, and distilled to obtain 2-pro...
PUM
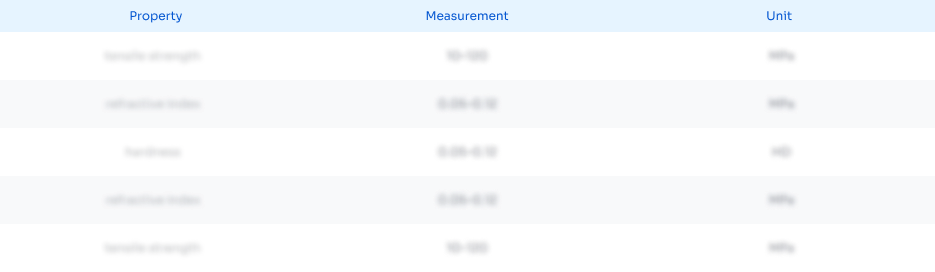
Abstract
Description
Claims
Application Information

- R&D Engineer
- R&D Manager
- IP Professional
- Industry Leading Data Capabilities
- Powerful AI technology
- Patent DNA Extraction
Browse by: Latest US Patents, China's latest patents, Technical Efficacy Thesaurus, Application Domain, Technology Topic, Popular Technical Reports.
© 2024 PatSnap. All rights reserved.Legal|Privacy policy|Modern Slavery Act Transparency Statement|Sitemap|About US| Contact US: help@patsnap.com