Tech. of preparing amino benz methyl-phenoxide by nitro methyl-phenoxide mixture catalyzing hydrogenation
A technology for nitroanisole and aminoanisole is applied in the field of preparing aminoanisole by catalytic hydrogenation of nitroanisole mixture, and can solve the problem of large discharge of waste water and waste residue, increased treatment cost and hidden danger of secondary pollution And other issues
- Summary
- Abstract
- Description
- Claims
- Application Information
AI Technical Summary
Problems solved by technology
Method used
Image
Examples
Embodiment 1
[0023] A process for preparing aminoanisole by catalytic hydrogenation of 2-nitroanisole, the process steps are as follows:
[0024] 1. Using methanol as a solvent, add 2-nitroanisole into a three-phase fixed-bed catalytic reactor with Raney-Ni as a catalyst. The amount of catalyst is 1.0% of the nitro compound, and the catalyst particles are 0.9 mm. Hydrogen is introduced into hydrogen to undergo a catalytic hydrogenation reduction reaction, and the hydrogen is prepared by methanol catalytic hydrogen production technology. During the reaction, the control temperature is 120 ° C, and the operating pressure is 4.0 MPa;
[0025] 2. After the catalytic hydrogenation reduction reaction is completed (the standard is to no longer consume hydrogen), solid-liquid separation is carried out after cooling and pressure relief, and the reaction material is transported to the catalyst recovery device, the blade filter device and the corresponding filter system to recover the catalyst. The c...
Embodiment 2
[0030] A process for preparing aminoanisole by catalytic hydrogenation of 4-nitroanisole, the process steps are as follows:
[0031] 1. Using methanol as the solvent, add 4-nitroanisole into the three-phase fluidized bed catalytic reactor with Raney-Ni as the catalyst, the amount of the catalyst is 4.5% of the nitro compound, the catalyst particle is 1.0mm, Catalytic hydrogenation reduction reaction occurs by feeding hydrogen, the control temperature during the reaction is 160°C, and the operating pressure is 6.0MPa;
[0032] 2. After the catalytic hydrogenation reduction reaction is completed (the standard is to no longer consume hydrogen), solid-liquid separation is carried out after cooling and pressure relief, and the reaction material is transported to the catalyst recovery device, the blade filter device and the corresponding filter system to recover the catalyst. The catalyst can be recycled, and the material removed from the catalyst enters the next step;
[0033] 3. ...
Embodiment 3
[0037] A process for preparing aminoanisole by catalytic hydrogenation of a mixture of 2-nitroanisole and 4-nitroanisole, the process steps are as follows:
[0038] (1) Take methanol as solvent, add 2-nitroanisole and 4-nitroanisole into the three-phase fixed-bed catalytic reactor using Raney-Ni as catalyst, the catalyst particle is 10.0mm, and then feed hydrogen Catalytic hydrogenation reduction reaction occurs, the control temperature during the reaction is 130°C, and the operating pressure is 4.8Mpa;
[0039] (2) After the catalytic hydrogenation reduction reaction is completed (with no more consumption of hydrogen as the standard), solid-liquid separation is carried out after cooling and pressure relief, and the reaction material is transported to the catalyst recovery device blade filter device and the corresponding filter system to recover the catalyst, The recovered catalyst can be recycled, and the material removed from the catalyst goes to the next step;
[0040] (3)...
PUM
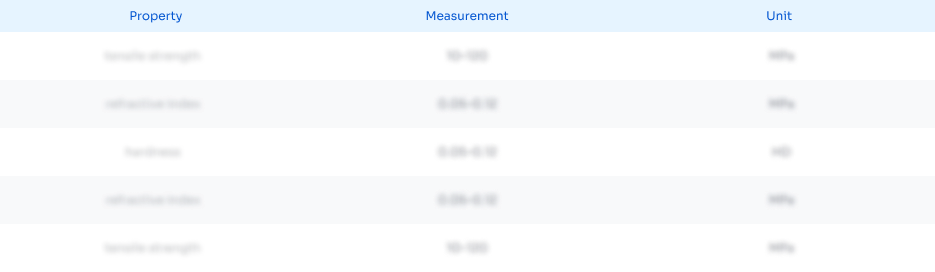
Abstract
Description
Claims
Application Information

- R&D
- Intellectual Property
- Life Sciences
- Materials
- Tech Scout
- Unparalleled Data Quality
- Higher Quality Content
- 60% Fewer Hallucinations
Browse by: Latest US Patents, China's latest patents, Technical Efficacy Thesaurus, Application Domain, Technology Topic, Popular Technical Reports.
© 2025 PatSnap. All rights reserved.Legal|Privacy policy|Modern Slavery Act Transparency Statement|Sitemap|About US| Contact US: help@patsnap.com